Safety improvement in a factory means that a company creates a workplace environment where the safety and health of employees are ensured, and it leads to improve retention rate, motivation, and productivity.
Solve these issues
with safety improvement in a factory
ISSUE
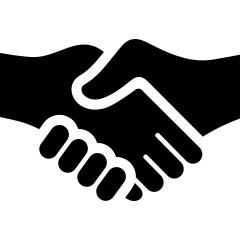
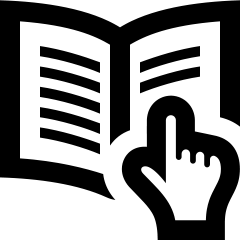
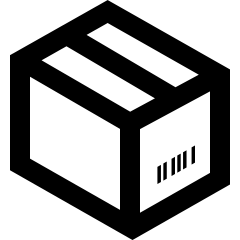
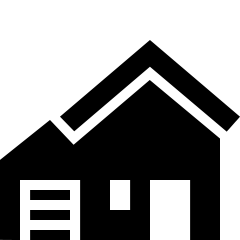
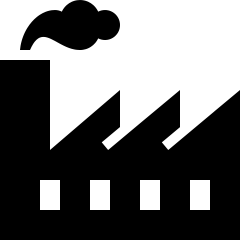
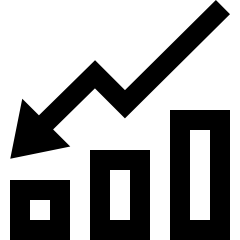
3 points
for safety improvement
FEATURES
-
1
5S (Sorting out, Setting in order, Shining, Standardizing, and Sustaining)
-
Maintaining a comfortable workplace through 5S (Sorting out, Setting in order, Shining, Standardizing, and Sustaining) is the basics of health and safety.
-
2
Establish correct working method
-
Correct working method (procedure manual) will be created and to be followed it.
-
3
Safety patrols
-
We conduct safety patrols to check operator’s behavior and the workplace environment.
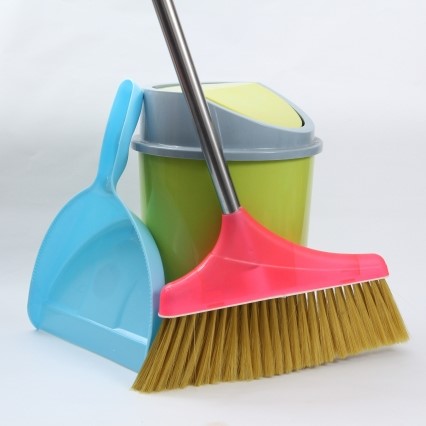
5S (Sorting out, Setting in order, Shining, Standardizing, and Sustaining)
5S is the basis of health and safety activities, and if we thoroughly implement 5S, we will see the workplace more carefully, and problems will become apparent. It leads to safety improvement of workplace, improvement of work efficiency, and prevention of the outflow of defective products.
The 5S points are: 1) Perform as a part of work, not as a special thing, 2) Participation of all employees, 3) Create 5S Map, 4) Implement 5S patrols.
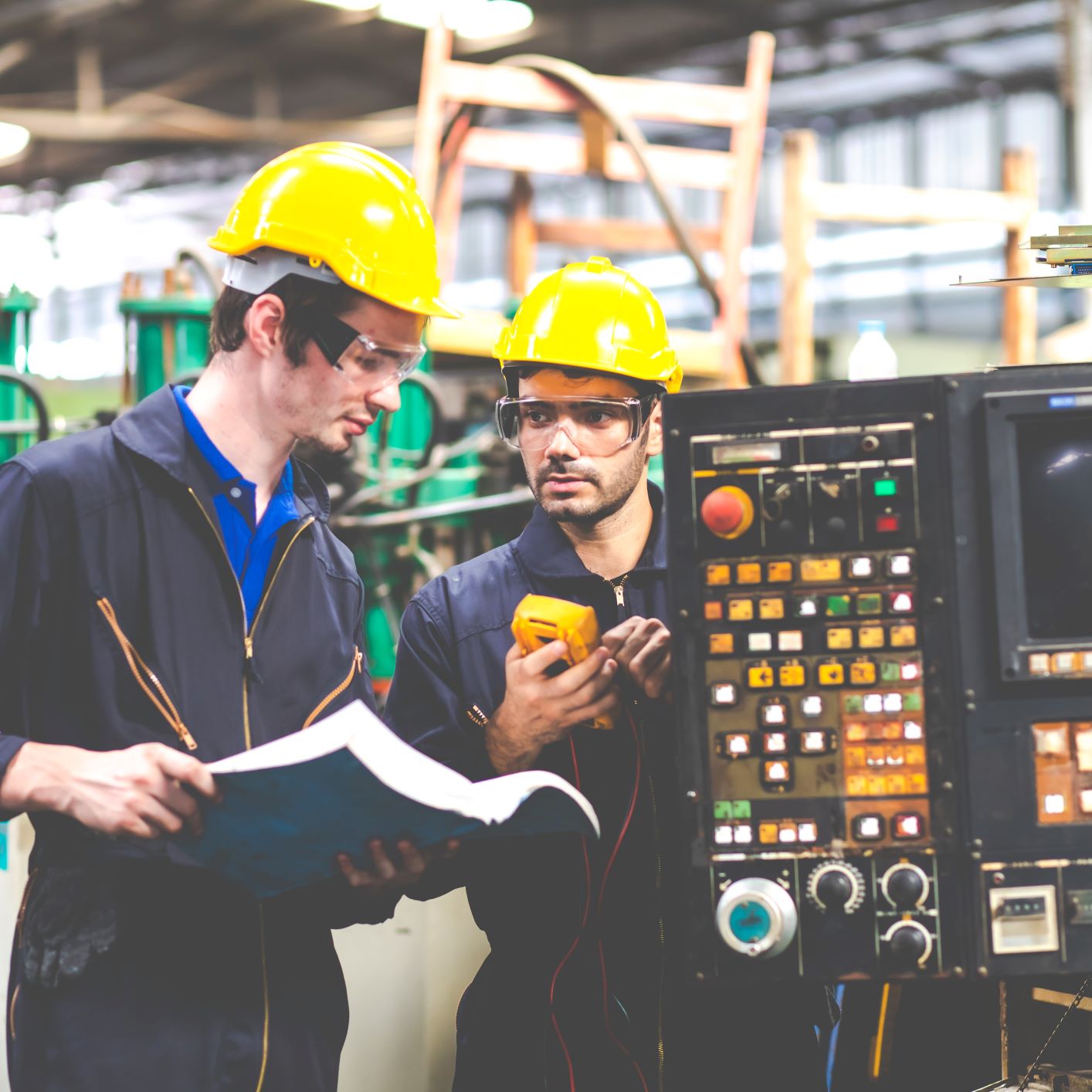
Establish correct working method
We create a procedure manual for each operation to train and check the operation order and contents, and describe the following items in the procedure manual. 1) Operation name, 2) Operation procedures, 3) Equipment, tools, and protective equipment to use, 4) Possible accidents that may occur and preventive measures / countermeasures, 5) Know-how, etc.
Points to let operators follow the procedures are: 1) Implement the operation training according to the procedure manual, 2) Check if the operation is done according to the procedure manual, 3) Store the procedure manual in the fixed place, 4) Review the operation procedures and the contents of the procedure manual regularly (When the procedures and operation contents are changed, when the equipment, tools and layout are changed, and when there is room for improvement in that procedure manual), 5) Implement the training again if the procedure manual is revised.
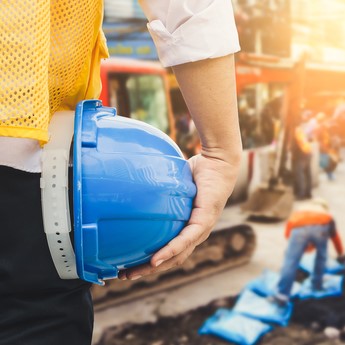
Safety patrols
Even if a procedure manual is created and training is implemented, operators may make a mistake in the operation procedures or take unsafe actions “carelessly” or “in a hurry”. In addition, there are cases where the shop floor is untidy because 5S has not been completed.
Therefore, we conduct safety patrols to check the operator behavior and the workplace environment, and point out any problems found in the shop floor and proceed improvements. The points of the safety patrols are: 1) Is there any unsafe behavior? 2) Is the equipment/device in a safe state? 3) Is 5S thoroughly implemented? etc.
Consultants from major companies
with experience in over 40 countries will respond.
Please feel free to contact us.
If you are in a hurry, please call us.
(Japan time)
Except for Saturday, Sunday, holidays, Year-End and New-Year holidays
Safety improvement Specialist
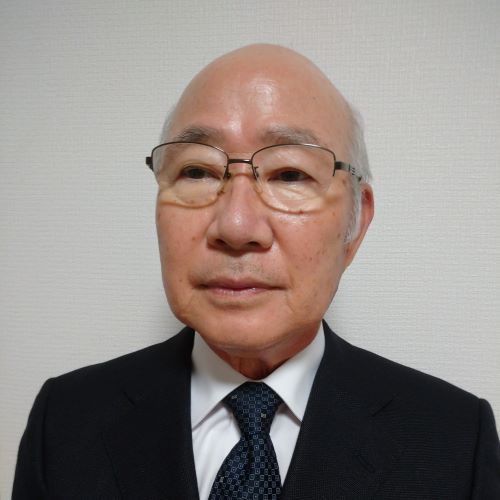
Kenichi Sawada
Sony Corp.
SAWADA puts into practice clean air technology, quality control and, moreover, manufacturing process improvement that should be controlled within the semiconductor manufacturing process (LED, CRD, LCE, SC wafer, etc.) He is a BCM (Business Continuity Management) as well as ISO9001 certificate acquisition expert.
Case example of Genba Kaizen Consulting RESULTS
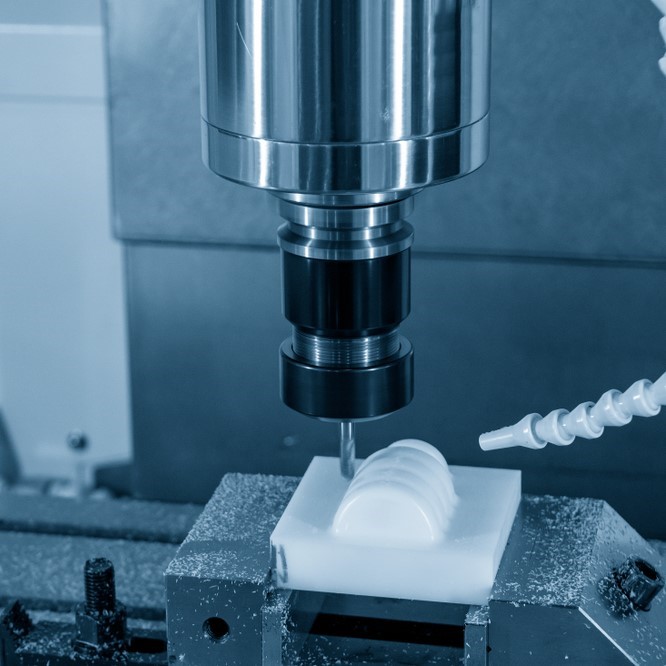
Acquired orders from two new customers
by improving quality.
We reduced most work-in-progress inventories and defective inventories, which were found throughout the factory, and reduced manpower, and now we almost no longer receive customer complaints that we had every month before. (Automobile industry / Plant manager)
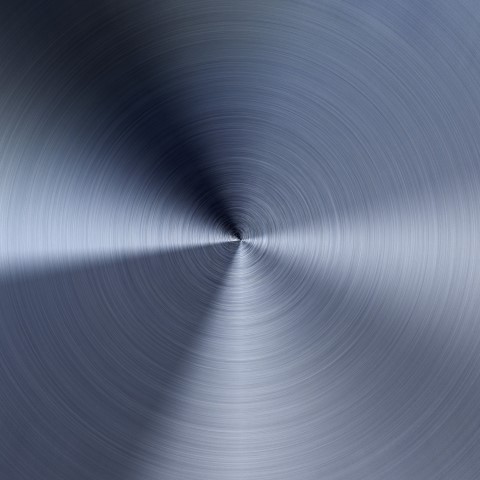
Turn the factory into a showroom
in order to improve profitability
We improved 250 cases out of 300 cases pointed out by the 5S patrol conducted for one year. The factory was realized to be the showroom and also achieved cost reduction of 30 million yen per year. (Metal processing / Director)
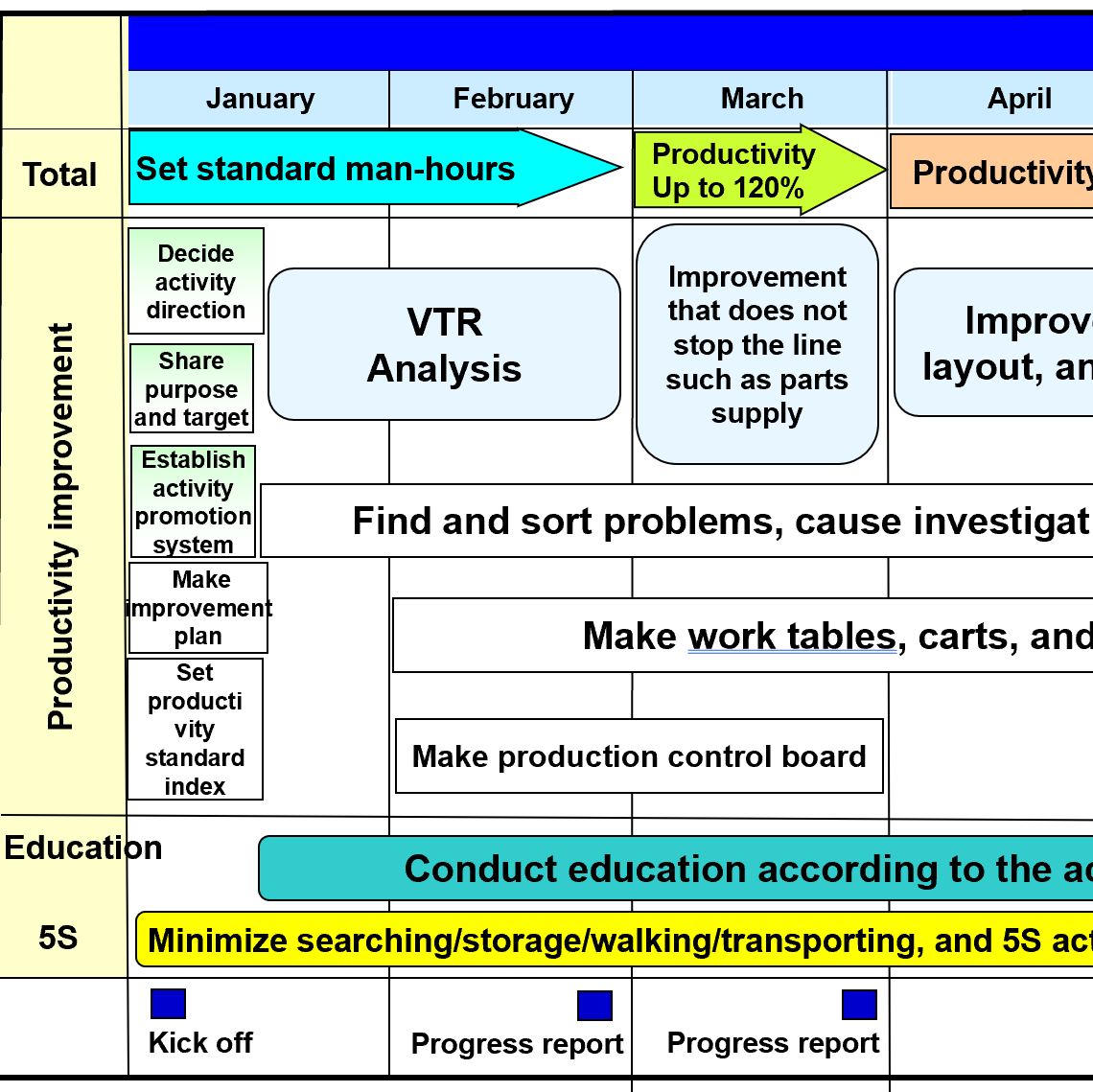
Productivity Up to 169.6%
by 6 months of improvement activities
the Japanese president decided to outsource a shop floor improvement consulting to have their shop floor checked, and asked us, Hirayama Consulting.(Auto parts manufacturer/Managing director)
3 reasons why we are chosen REASON
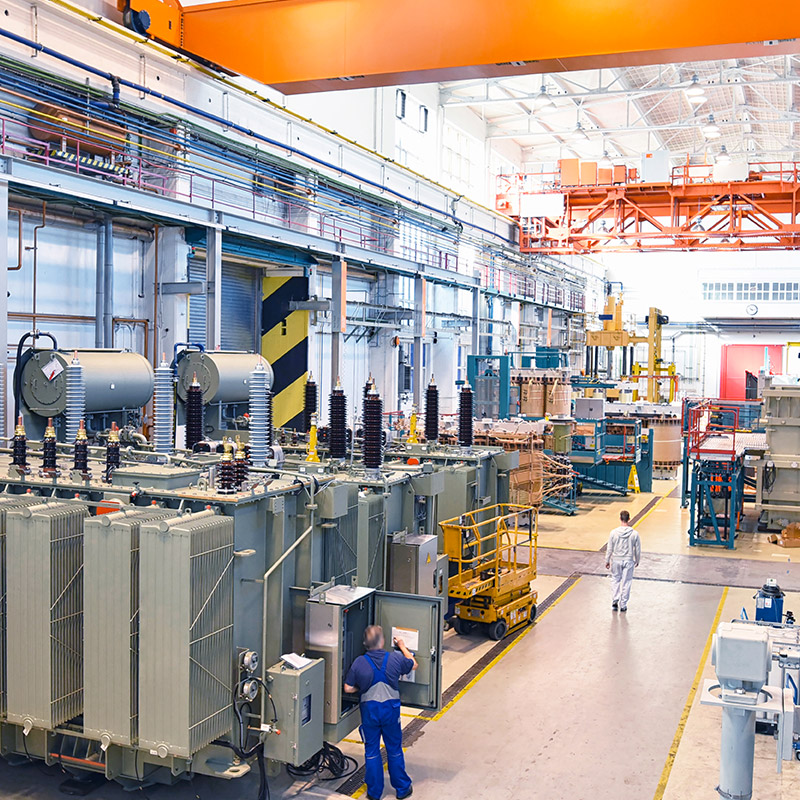
REASON 1
Improvement experience of
more than 1,500 companies in 40 countries
There must be the shop floor issues that cannot be solved by your own company alone. Improvements and reforms for manufacturing industry to survive, regardless of country or industry, need development of your human resources through practical experiences of improvement, and strengthening of your production system base.
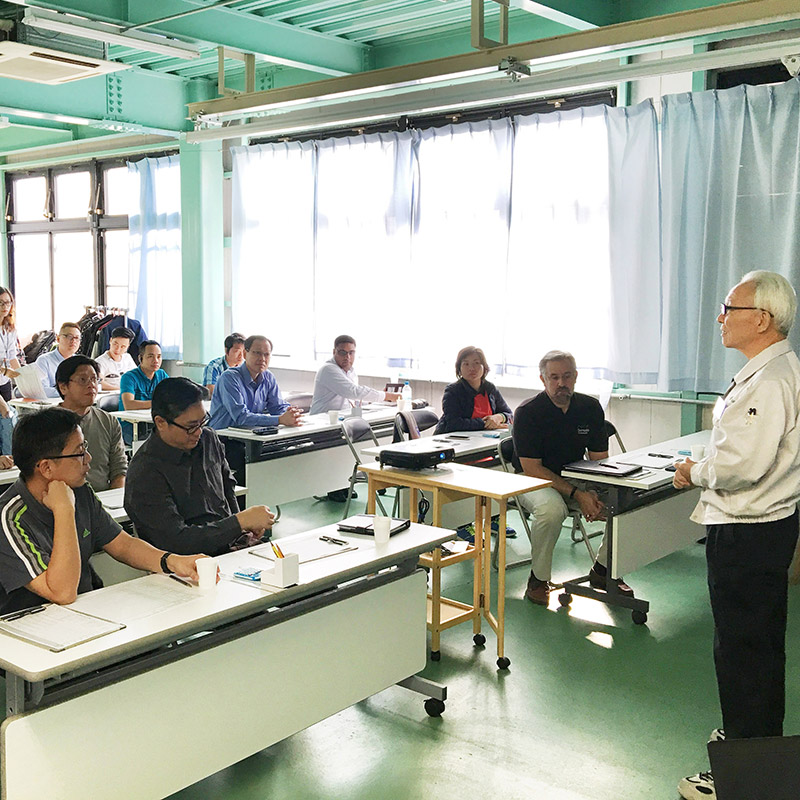
REASON 2
Consulting that shop floor workers
acknowledge our superiority and be pleased
In conventional consulting styles, there was a distance between consultant and the shop floor because it was promoted mainly consultant and management executives. Our consultant can provide a guidance without a distance between consultant and the shop floor through the guidance based on the "seeds of improvement" in a concrete way, instead of "finding fault" like a critic.
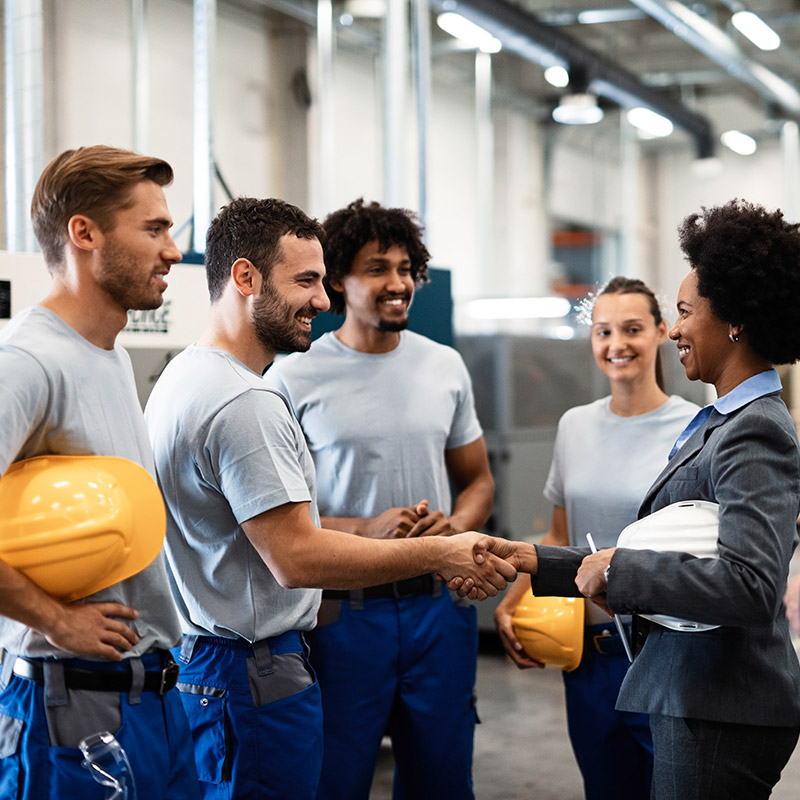
REASON 3
Continuous improvement will continue
even after the end of guidance
While strengthening "human resource development", we focus on the "overall flow" from design to purchasing, manufacturing, logistics, and production control, and provide guidance that matches the actual situation of your company. Continuous improvement will continue even after the end of guidance through the guidance that is acceptable to the shop floor workers.