Training Title | Target | Purpose | Place | Schedule/Period |
---|---|---|---|---|
Toyota way – problem solving (improvement power) – August, 30 | Gemba leader / Kaizen(improvement) promoter / management supervisors | 2022/08/30 10:00 | ||
5S training: 5S concepts and production efficiency August, 25 | Gemba leader / Kaizen(improvement) promoter / management supervisors | 2022/08/25 10:00 | ||
Toyota Production System’s waste-free quality control – August, 11 | Gemba leader / Kaizen(improvement) promoter / management supervisors | 2022/08/11 10:00 | ||
Toyota way – how to teach the work – methodology – August, 9th | Managers and supervisors | 2022/08/09 10:00 | ||
Training for new employees: Industry Basics Aspects and Mindset August, 8th | New employee / New graduate | 2022/08/08 09:30 | ||
Toyota way – problem solving (improvement power) July, 28 | Gemba leader / Kaizen(improvement) promoter / management supervisors | 2022/07/28 10:00 | ||
5S training: 5S concepts and production efficiency July, 21 | Gemba leader / Kaizen(improvement) promoter / management supervisors | 2022/07/21 10:00 | ||
Toyota way – problem solving (improvement power) July, 14 | Gemba leader / Kaizen(improvement) promoter / management supervisors | 2022/07/14 10:00 | ||
Toyota way – how to teach the work – methodology – July, 12th | Managers and supervisors | 2022/07/12 10:00 | ||
Training for new employees: Industry Basics Aspects and Mindset July 11th | New employee / New graduate | 2022/07/11 09:30 | ||
Toyota way – problem solving (improvement power) July, 7 | Gemba leader / Kaizen(improvement) promoter / management supervisors | 2022/07/07 10:00 | ||
Toyota Production System’s waste-free quality control – June, 30 | Managers and supervisors | 2022/06/30 10:00 | ||
5S training: 5S concepts and production efficiency June 23rd | Gemba leader / Kaizen(improvement) promoter / management supervisors | 2022/06/23 10:00 | ||
Toyota way – how to teach the work – methodology – June, 14 | Managers and supervisors | 2022/06/14 10:00 | ||
Training for new employees: Industry Basics Aspects and Mindset June, 13 | New employee / New graduate | 2022/06/13 09:30 | ||
Toyota way – problem solving (improvement power) – May, 26 | Gemba leader / Kaizen(improvement) promoter / management supervisors | 2022/05/26 10:00 | ||
【WEB】TPS JISSEN DOJO May, 25 | Manager / supervisor, improvement promoter, production engineer | 2022/05/25 09:00 | ||
5S training: 5S concepts and production efficiency May, 19 | Gemba leader / Kaizen(improvement) promoter / management supervisors | 2022/05/19 10:00 | ||
Toyota Production System’s waste-free quality control – May 12 | Managers and supervisors | 2022/05/12 15:00 | ||
Toyota way – how to teach the work – methodology – May, 10 | Managers and supervisors | 2022/05/10 10:00 | ||
Training for new employees: Industry Basics Aspects and Mindset May, 9 | New employee / New graduate | 2022/05/09 09:30 | ||
Toyota way – problem solving (improvement power) April, 28 | Gemba leader / Kaizen(improvement) promoter / management supervisor | 2022/04/28 10:00 | ||
【WEB】TPS JISSEN DOJO April, 27 | Manager / supervisor, improvement promoter, production engineer | 2022/04/27 09:00 | ||
5S training: 5S concepts and production efficiency April, 21 | Gemba leader / Kaizen(improvement) promoter / management supervisors | 2022/04/21 10:00 | ||
Toyota Production System’s waste-free quality control – April, 14 | Managers and supervisors | 2022/04/14 15:00 | ||
Toyota way – how to teach the work – methodology – April 12th | Managers and supervisors | 2022/04/12 10:00 | ||
Training for new employees: Industry Basics Aspects and Mindset April, 4 | New employee / New graduate | 2022/04/04 09:30 | ||
Toyota way – problem solving (improvement power) March 24 | Gemba leader / Kaizen(improvement) promoter / management supervisors | 2022/03/24 10:00 | ||
【WEB】TPS JISSEN DOJO March, 23 | Managers/supervisor, Kaizen and improvement promotion office trainers, production engineer | 2022/03/23 09:00 | ||
5S training: 5S concepts and production efficiency March 17 | Gemba leader / Kaizen(improvement) promoter / management supervisors | 2022/03/17 10:00 |
3 reasons why we are chosen REASON
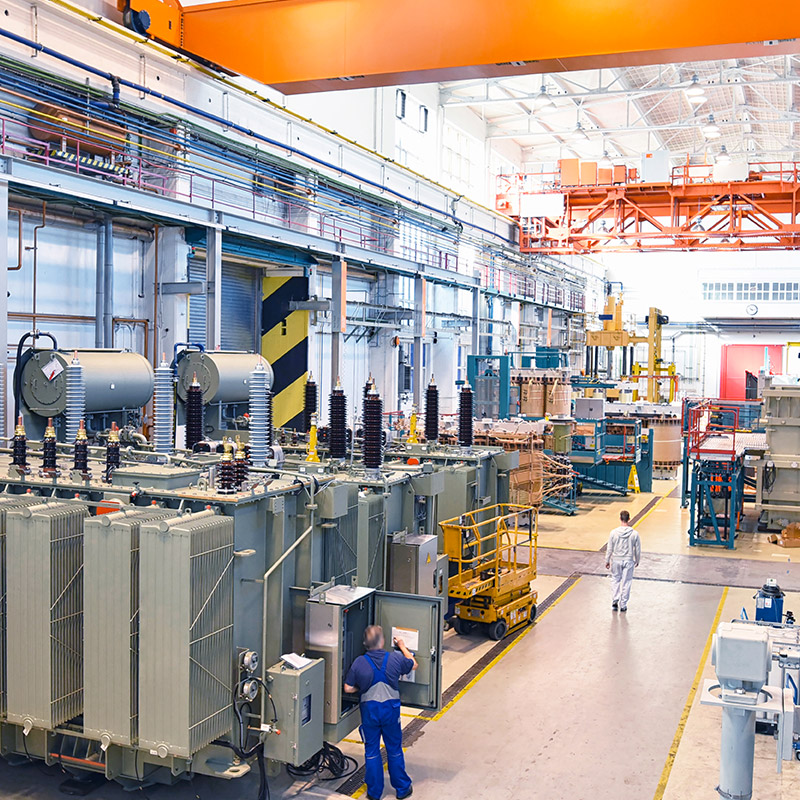
REASON 1
Improvement experience of
more than 1,500 companies in 40 countries
There must be the shop floor issues that cannot be solved by your own company alone. Improvements and reforms for manufacturing industry to survive, regardless of country or industry, need development of your human resources through practical experiences of improvement, and strengthening of your production system base.
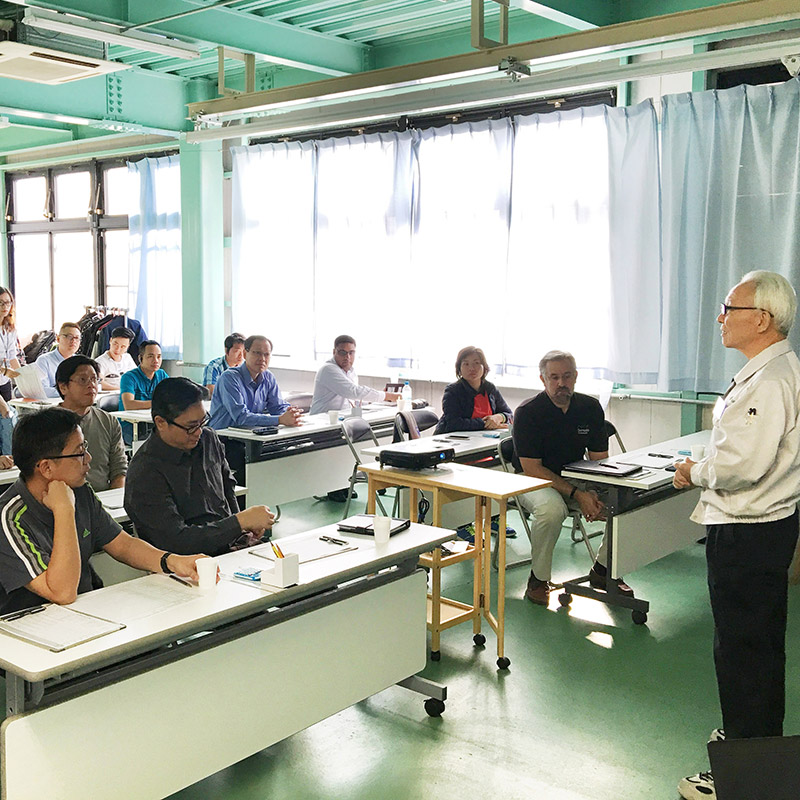
REASON 2
Consulting that shop floor workers
acknowledge our superiority and be pleased
In conventional consulting styles, there was a distance between consultant and the shop floor because it was promoted mainly consultant and management executives. Our consultant can provide a guidance without a distance between consultant and the shop floor through the guidance based on the “seeds of improvement” in a concrete way, instead of “finding fault” like a critic.
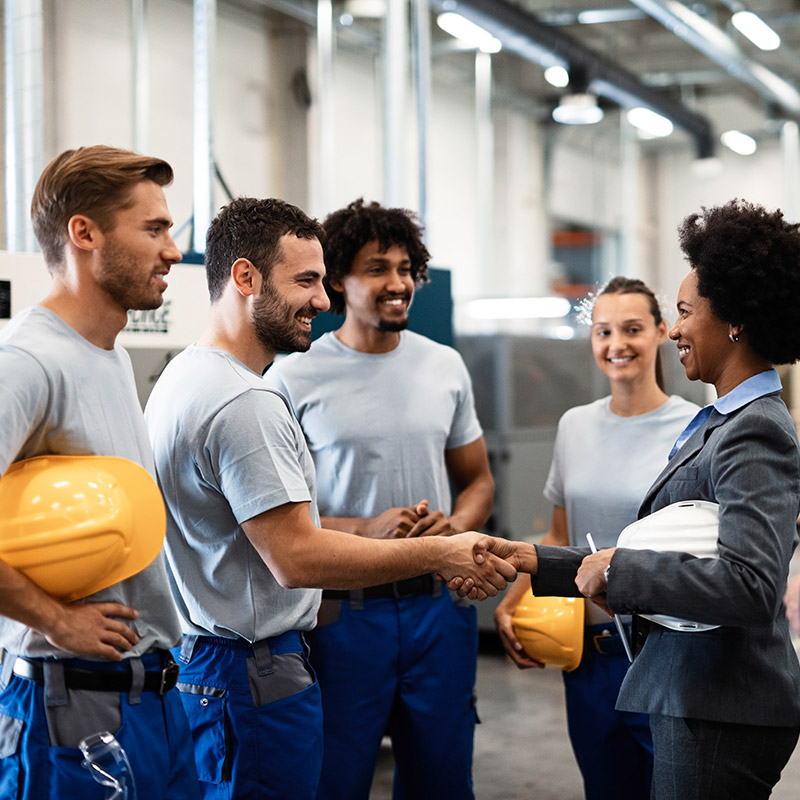
REASON 3
Continuous improvement will continue
even after the end of guidance
While strengthening “human resource development”, we focus on the “overall flow” from design to purchasing, manufacturing, logistics, and production control, and provide guidance that matches the actual situation of your company. Continuous improvement will continue even after the end of guidance through the guidance that is acceptable to the shop floor workers.