Training Features
5S is closely tied to production efficiency, and it is impossible to ignore a situation where 5S is not well-established. To understand the relationship between 5S and production efficiency and determine the appropriate 5S practices, a TPS officially certified trainer, who has supported Toyota’s production sites for over 40 years, will give clear lectures incorporating case studies and hands-on activities.
Application process
The schedule and location will be determined in consultation with you.
Review
- It felt specific and immediately applicable, and I am very excited to put it into practice in the workplace.
- I found it very beneficial to discover that my understanding of basics like the ‘5Ws’ and the ‘5 Whys analysis’ was slightly different from what I had thought, leading to new insights.
- I was able to gain an essential understanding of the 5S concepts, not just a superficial one. The specific measures provided were easy to visualize and understand.
- The lecture was very easy to understand, as we learned how to approach 5S through various case studies.
- I was able to understand the essence of 5S. I now recognize the good points of our current 5S activities as well as the areas that need improvement, and I plan to implement these changes.
Lineup
Training Title | Target | Purpose | Place | Schedule/Period |
---|---|---|---|---|
5S training: 5S concepts and production efficiency | Gemba leader / Kaizen(improvement) promoter / management supervisors | To be decided upon consultation |
3 reasons why we are chosen
REASON
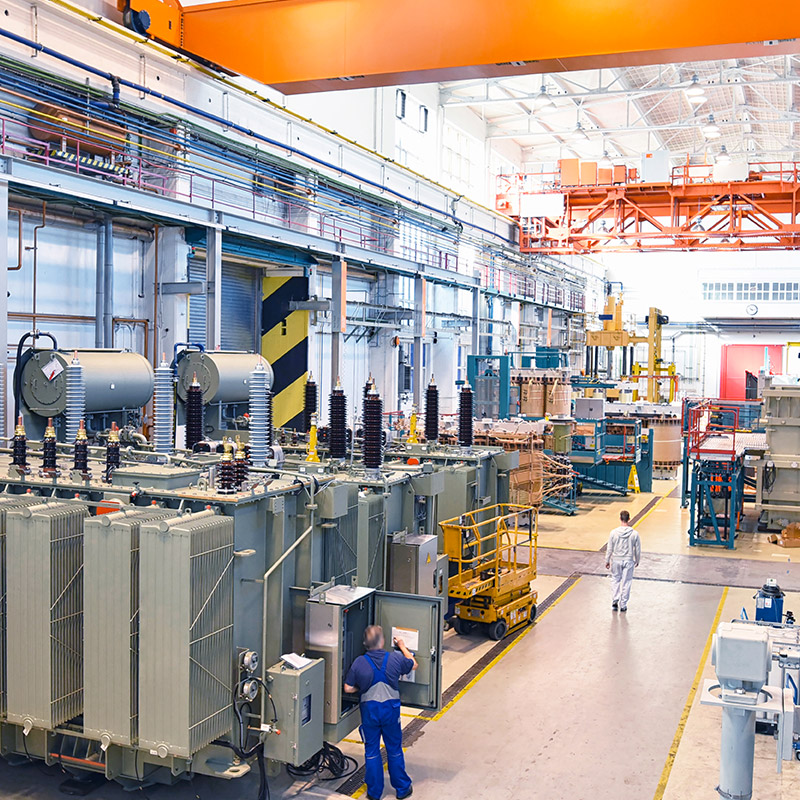
REASON 1
Improvement experience of
more than 1,500 companies in 40 countries
There must be the shop floor issues that cannot be solved by your own company alone. Improvements and reforms for manufacturing industry to survive, regardless of country or industry, need development of your human resources through practical experiences of improvement, and strengthening of your production system base.
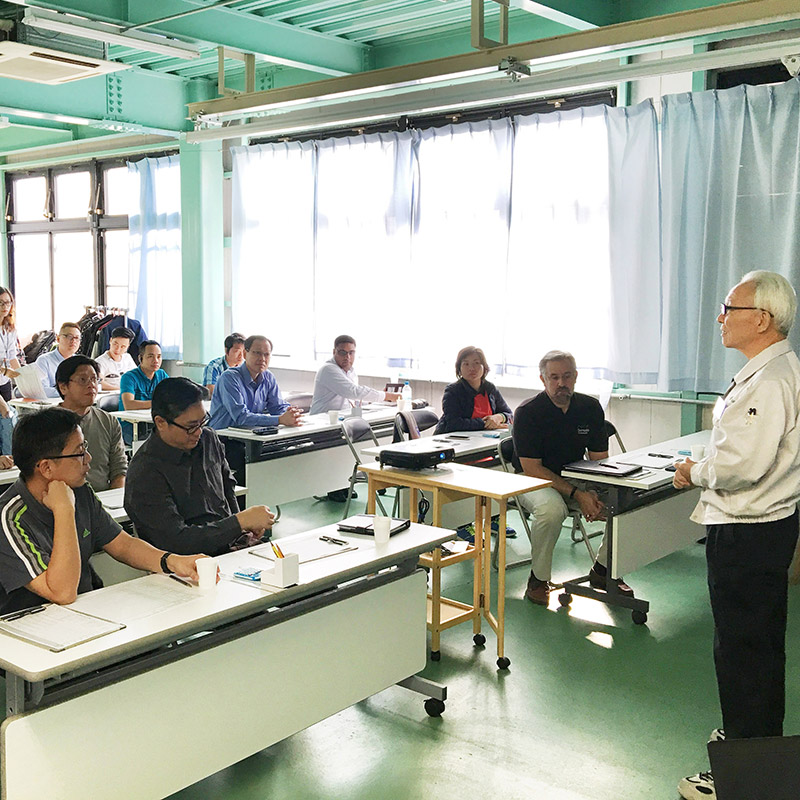
REASON 2
Consulting that shop floor workers
acknowledge our superiority and be pleased
In conventional consulting styles, there was a distance between consultant and the shop floor because it was promoted mainly consultant and management executives. Our consultant can provide a guidance without a distance between consultant and the shop floor through the guidance based on the “seeds of improvement” in a concrete way, instead of “finding fault” like a critic.
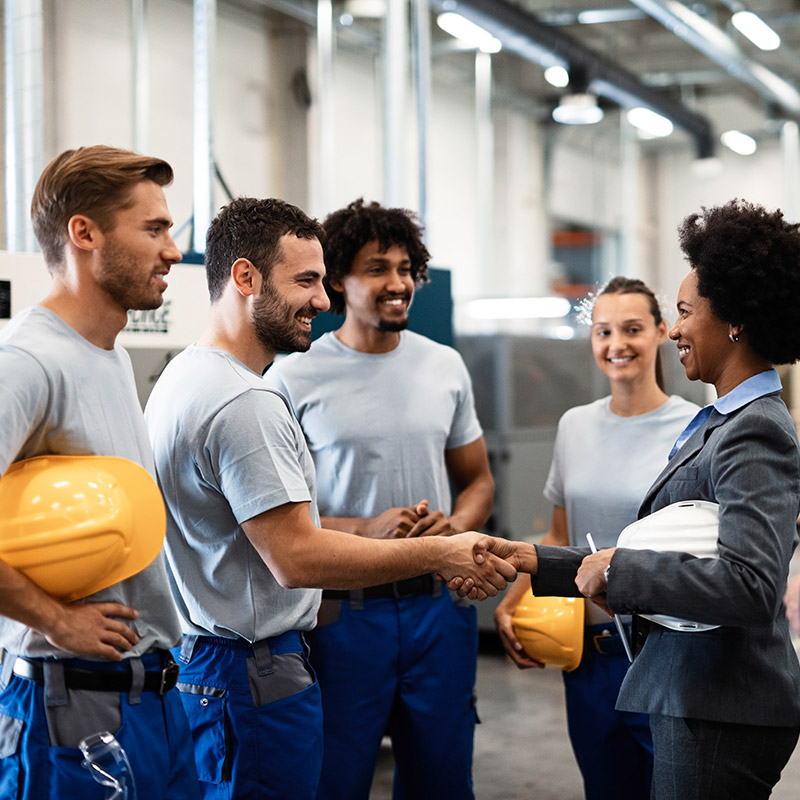
REASON 3
Continuous improvement will continue
even after the end of guidance
While strengthening “human resource development”, we focus on the “overall flow” from design to purchasing, manufacturing, logistics, and production control, and provide guidance that matches the actual situation of your company. Continuous improvement will continue even after the end of guidance through the guidance that is acceptable to the shop floor workers.