Training Features
The role of general workers in the production site is very significant. Their responsibilities include daily production activities, 5S, equipment inspection, safety initiatives, quality maintenance, and improvement activities, among others. However, systematic education for these crucial positions is surprisingly not being conducted as much as it should be.
This seminar is designed for employees supporting Japan’s manufacturing sites. It will clearly explain what each level needs to learn, incorporating exercises and group discussions throughout.
Application process
The schedule and location will be determined in consultation with you.
Review
- I am eager to return to the site and quickly implement what I have learned.
- Since it was a training specialized in personnel education for manufacturing sites, I felt that all three sessions were worthwhile.
- I gained a good understanding of the ‘eye for identifying waste’ and ‘improvement methods’ for betterment. Although I am not in the manufacturing department, the TPS concepts were very informative and provided valuable experience.
- The content was extensive. The combination of lectures, practical exercises, case studies, and video presentations was effective. Through the bicycle assembly work, I was able to thoroughly understand the lecture content.
Lineup
Training Title | Target | Purpose | Place | Schedule/Period |
---|---|---|---|---|
On-Site Practical Training for Enhancing Production Capabilities
Three-Session Course: Lectures, Hands-On Training, and Practical Application
|
For All Members of the Manufacturing Department | Cultivating the Ability to Identify Waste and Mastering Skills to Drive Cost-Reduction Activities** | At Your Designated Location |
To be decided upon consultation
Three-Session Course (3–4 Hours per Session)
The course structure can be customized upon request. |
3 reasons why we are chosen
REASON
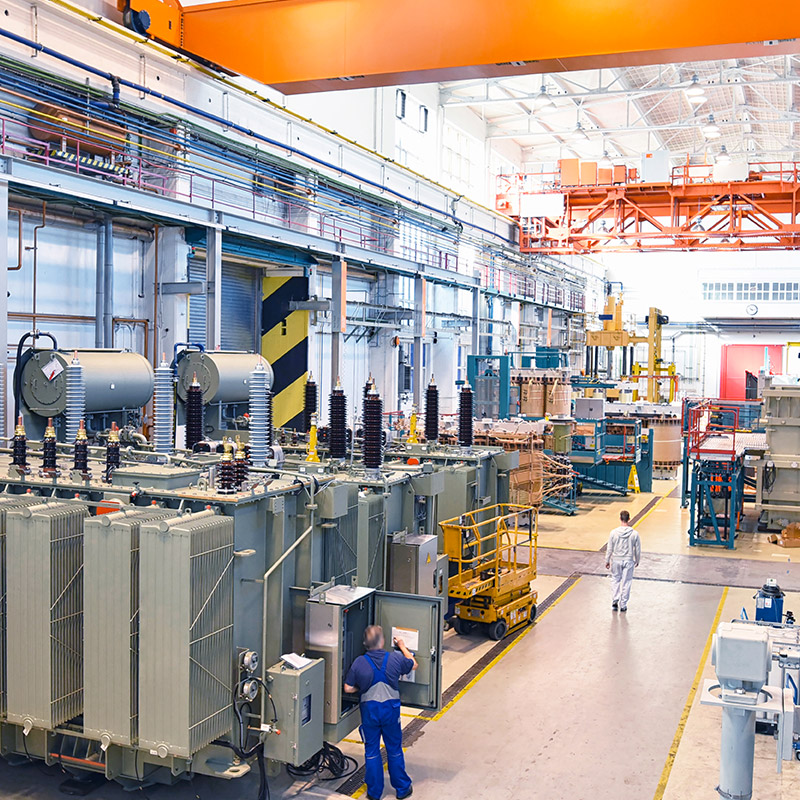
REASON 1
Improvement experience of
more than 1,500 companies in 40 countries
There must be the shop floor issues that cannot be solved by your own company alone. Improvements and reforms for manufacturing industry to survive, regardless of country or industry, need development of your human resources through practical experiences of improvement, and strengthening of your production system base.
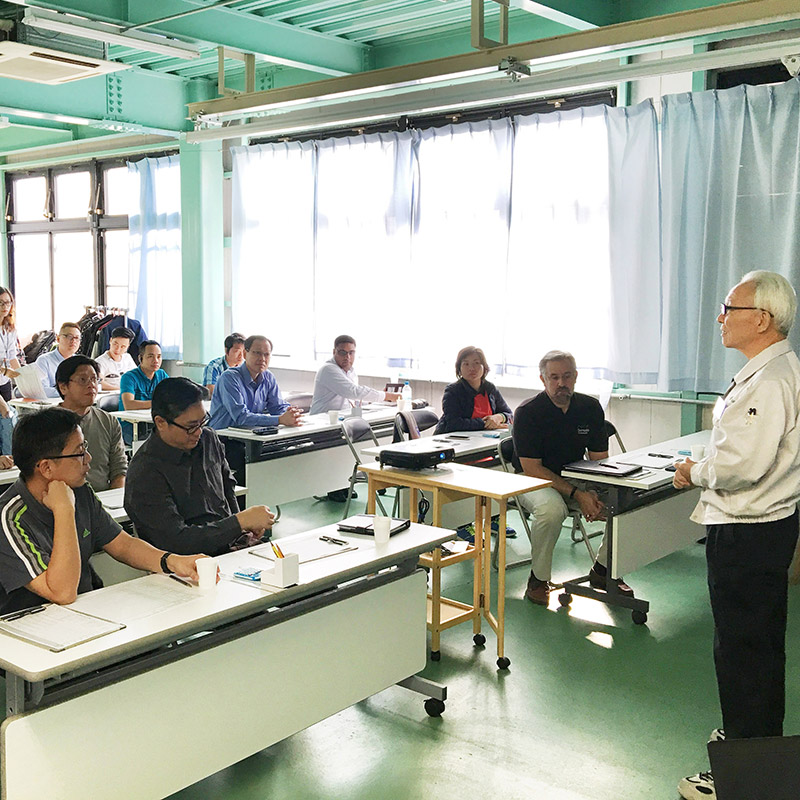
REASON 2
Consulting that shop floor workers
acknowledge our superiority and be pleased
In conventional consulting styles, there was a distance between consultant and the shop floor because it was promoted mainly consultant and management executives. Our consultant can provide a guidance without a distance between consultant and the shop floor through the guidance based on the “seeds of improvement” in a concrete way, instead of “finding fault” like a critic.
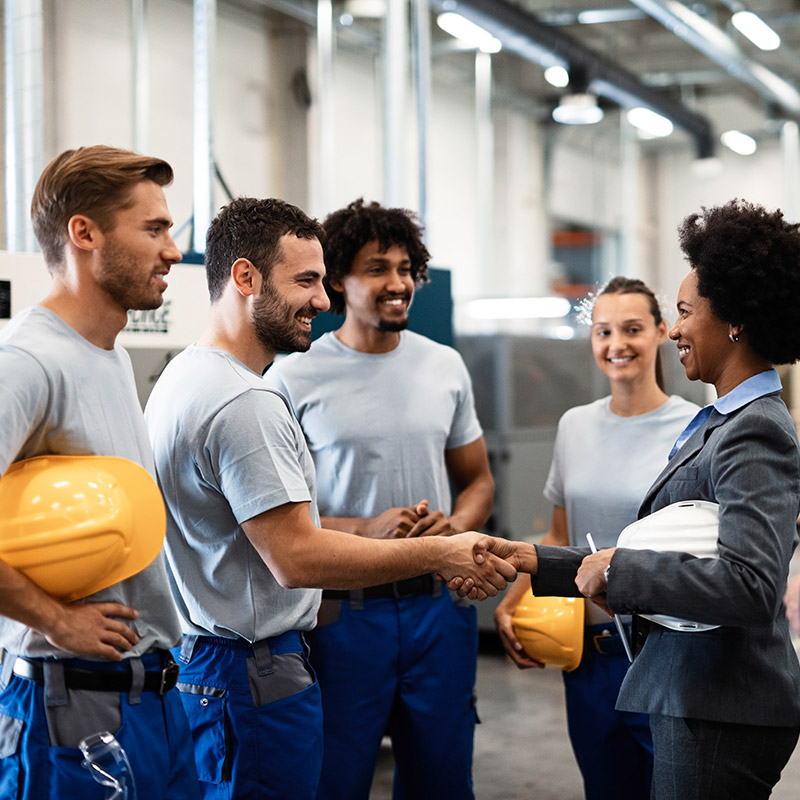
REASON 3
Continuous improvement will continue
even after the end of guidance
While strengthening “human resource development”, we focus on the “overall flow” from design to purchasing, manufacturing, logistics, and production control, and provide guidance that matches the actual situation of your company. Continuous improvement will continue even after the end of guidance through the guidance that is acceptable to the shop floor workers.