We introduce some of the achievements that our experienced consultants have provided highly effective consulting both in Japan and abroad based on the TPS (Toyota Production System), cooperating with the work implementation team
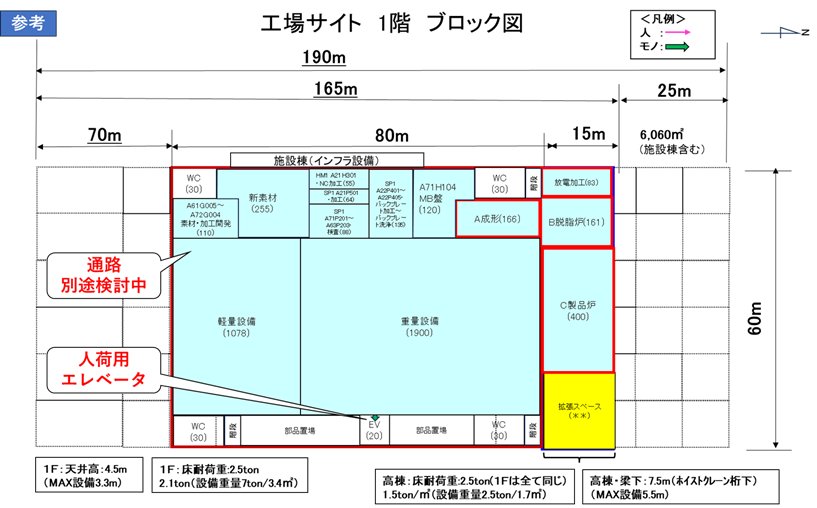
Case Study: Improvement of a New Factory Layout
[Results]Establishing a New Plant to Increase Production Capacity by 40%
[Purpose]
生産性 向上
電機・電子
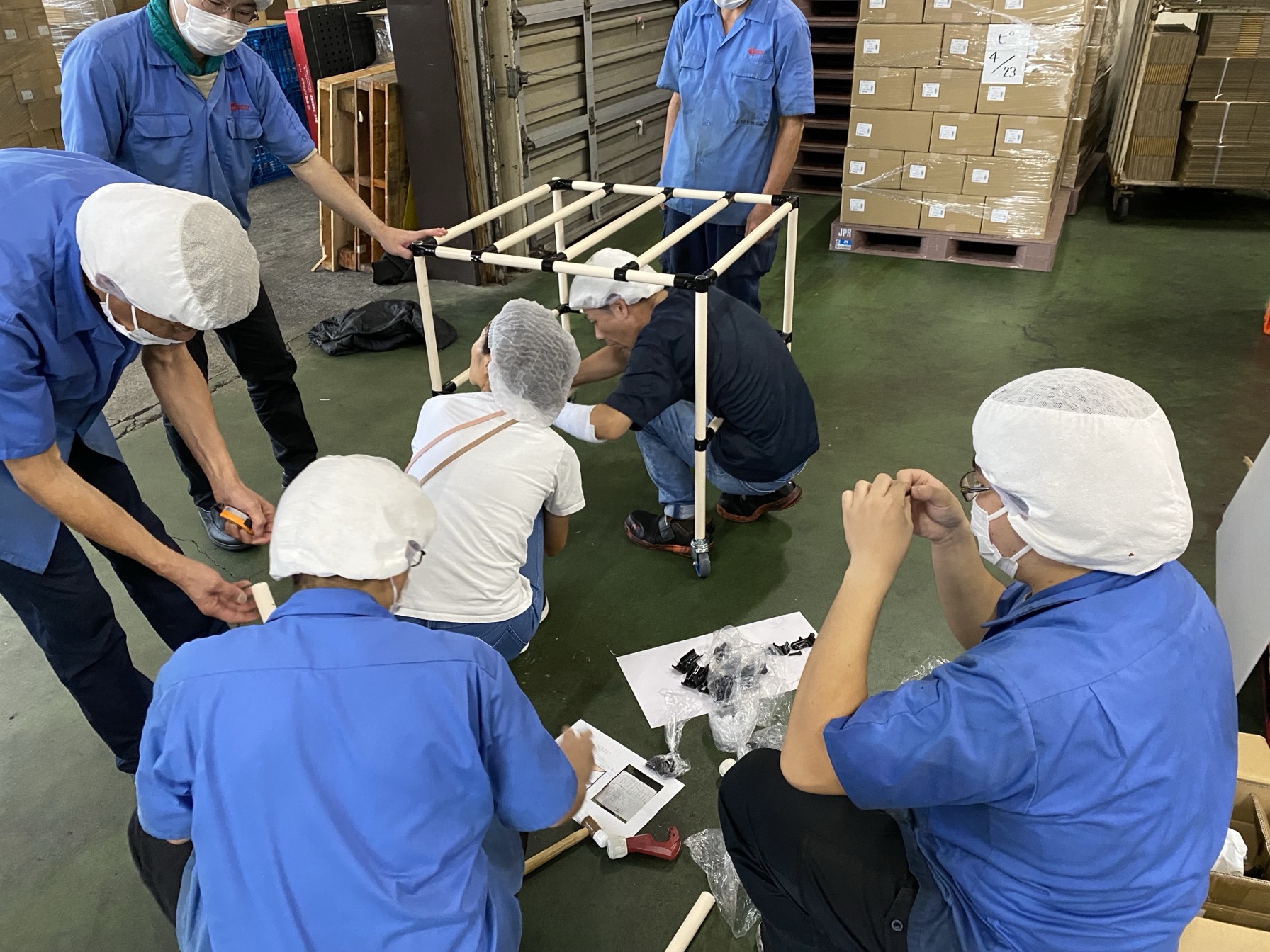
Case Study: Workbench Improvement in a Food Factory
[Results]・Bending Work: 3,000 to 5,000 times per day → 0 times
・Work Improvement: Reduction of 48 to 120 minutes per day [Industry]
食品
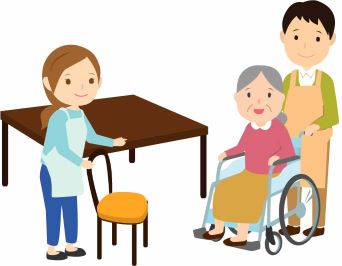
Preliminary On-Site Assessment of Care Facilities: Part 2
[Results]・Increase in the number of people that can be accommodated by 5
・Improvement of staff working conditions
・Reduction of task time to approximately one-third
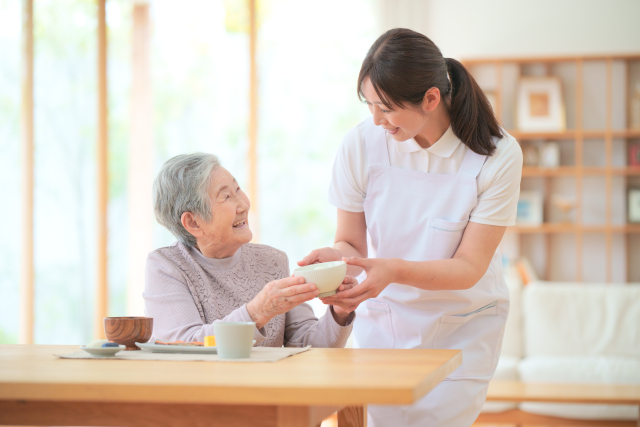
Preliminary On-Site Assessment of Care Facilities: Part 1
[Results]・Utilization space increased sixfold
・Reorganization of layout
・New service ideas (boosting staff motivation)
[Industry]
その他
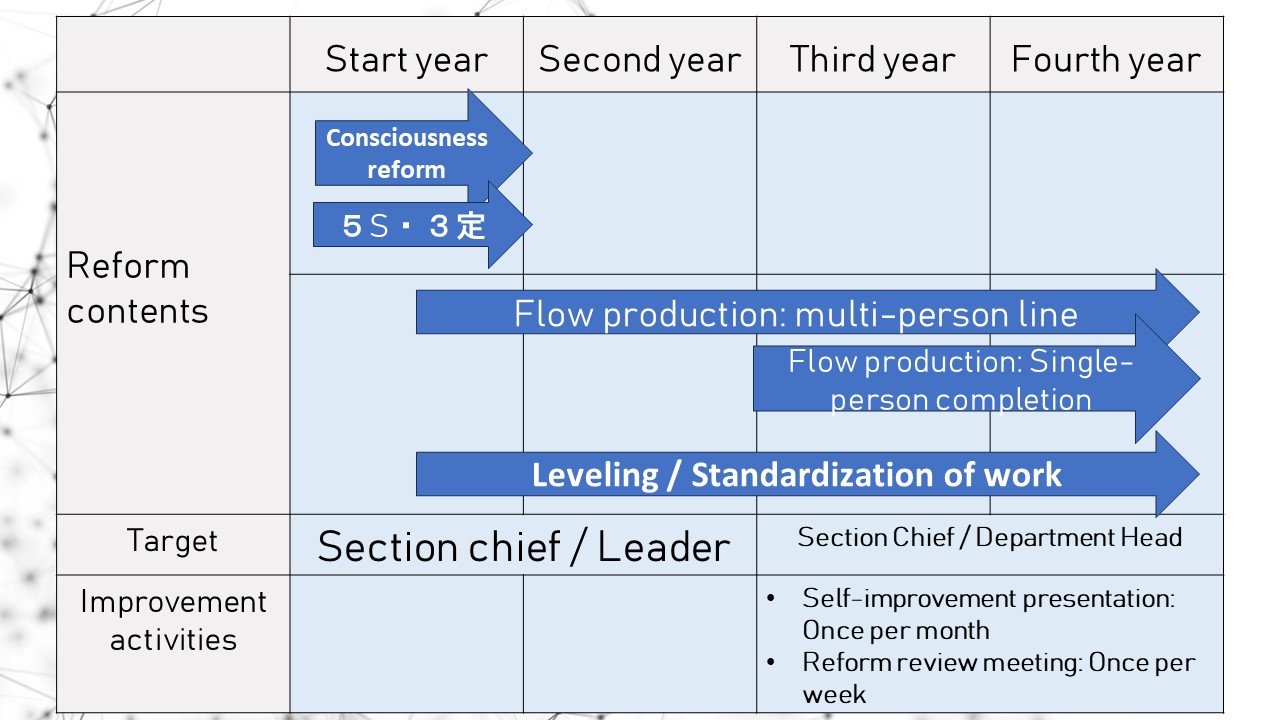
On-Site Improvement : 40,000 Cases in 4 Years
[Results]Productivity 26%UP
Defect rate: Less than 0.1%
Lead time 16-hour reduction
On-time delivery rate of 98%
[Purpose]
Profitability improvement
Electrical and electronic
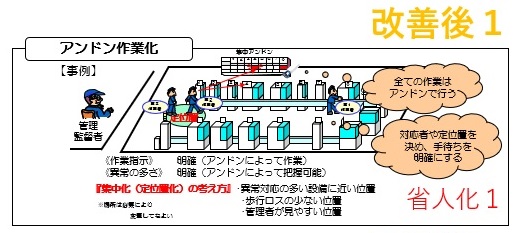
[Online Consulting Case Study] 30% Productivity Increase in One Year
[Results]Improvement of Setup Change Operations
(Before Improvement)92 minutes 34 seconds→(After Improvement)53 minutes 2 seconds (reduced by 39 minutes 32 seconds)
[Purpose]
Profitability improvement
Others

Improvement Case Study in a Cleanroom
[Results]- 2S (Sort and Set in order) was thoroughly implemented, leading to an improvement in the defect rate.
[Purpose]
Quality improvement
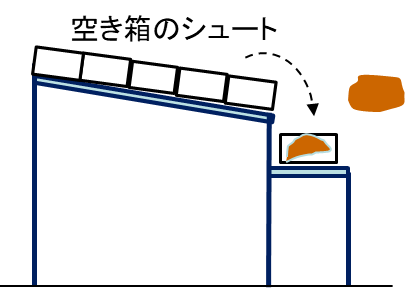
Immediate Improvement Examples in a Food Factory
[Results]From 277 pieces per hour → 450 pieces per hour
Productivity Increase by 62%
[Purpose]
Profitability improvement
food
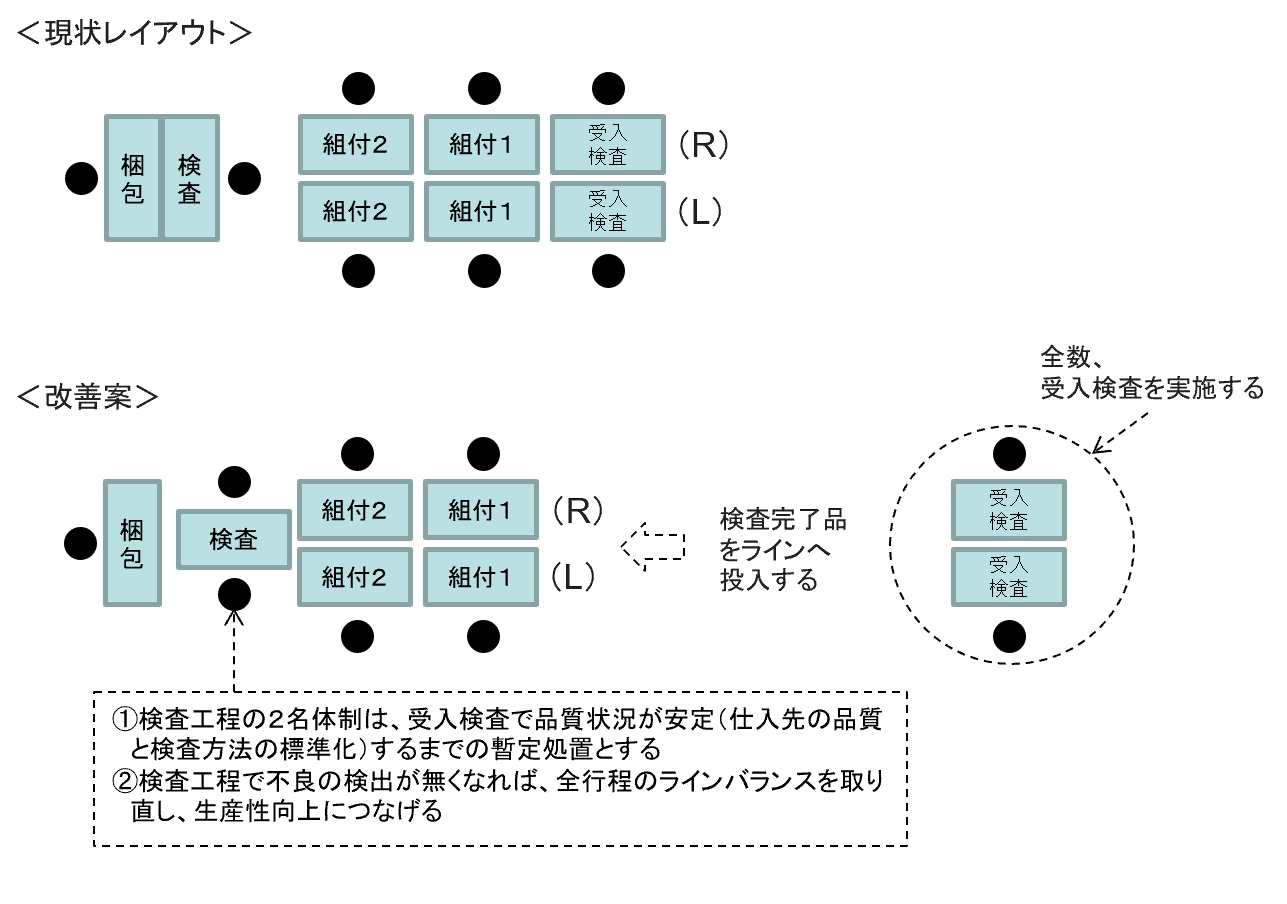
Case example of factory diagnosis (Simple type)
[Results]- Issues that customers could not see or notice can be identified
- Improvement plan that combines measures for the shop floor improvement and employees’ awareness improvement
[Purpose]
Human resource developmentProfitability improvement
Automobile
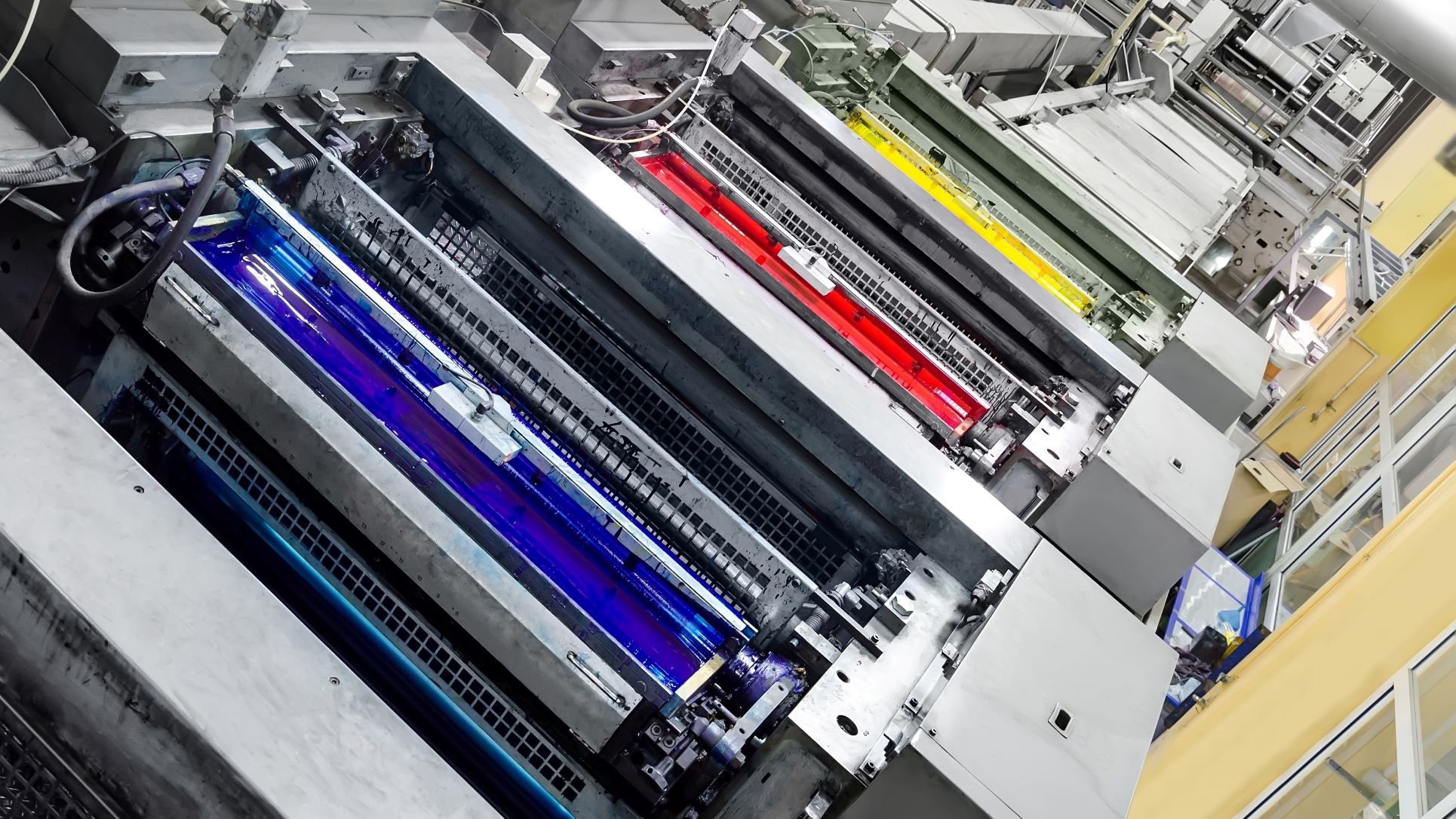
Kaizen Case: 3-Years period on Developing Kaizen Personnel who can Promote Voluntary Improvement
[Results]24% Reduction in End-of Month Inventory
44% Reduction in Warehouse Logistics
Lead Time Shortening by 5 Days
<Quality Technology Department/ Quality Control Section>
45% Reduction of Defects Rate in Total of All 10 Supplier Company
[Purpose]
Human resource development
Electrical and electronic
3 reasons why we are chosen
REASON
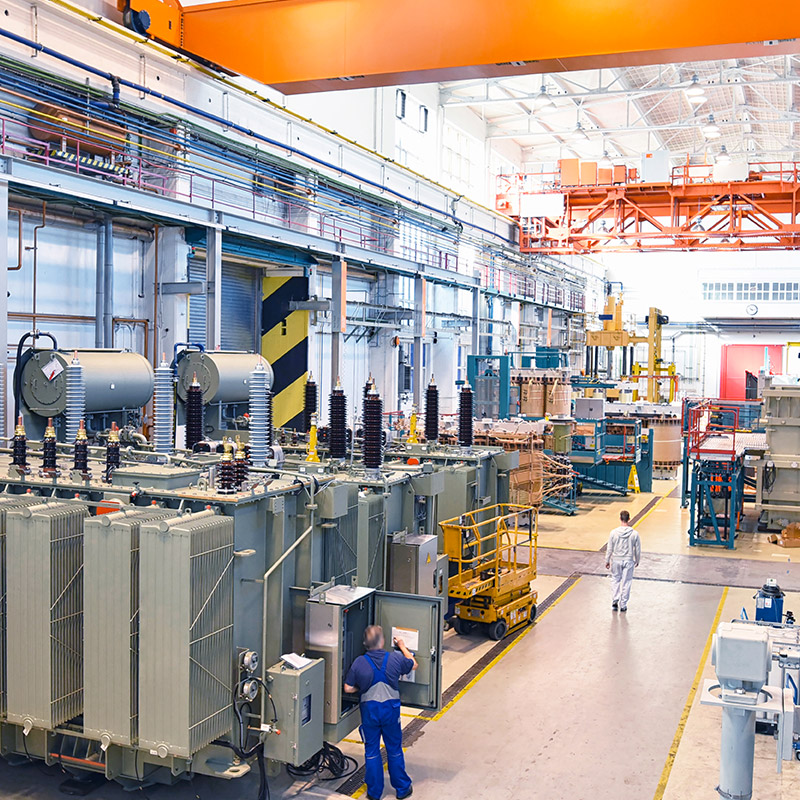
REASON 1
Improvement experience of
more than 1,500 companies in 40 countries
There must be the shop floor issues that cannot be solved by your own company alone. Improvements and reforms for manufacturing industry to survive, regardless of country or industry, need development of your human resources through practical experiences of improvement, and strengthening of your production system base.
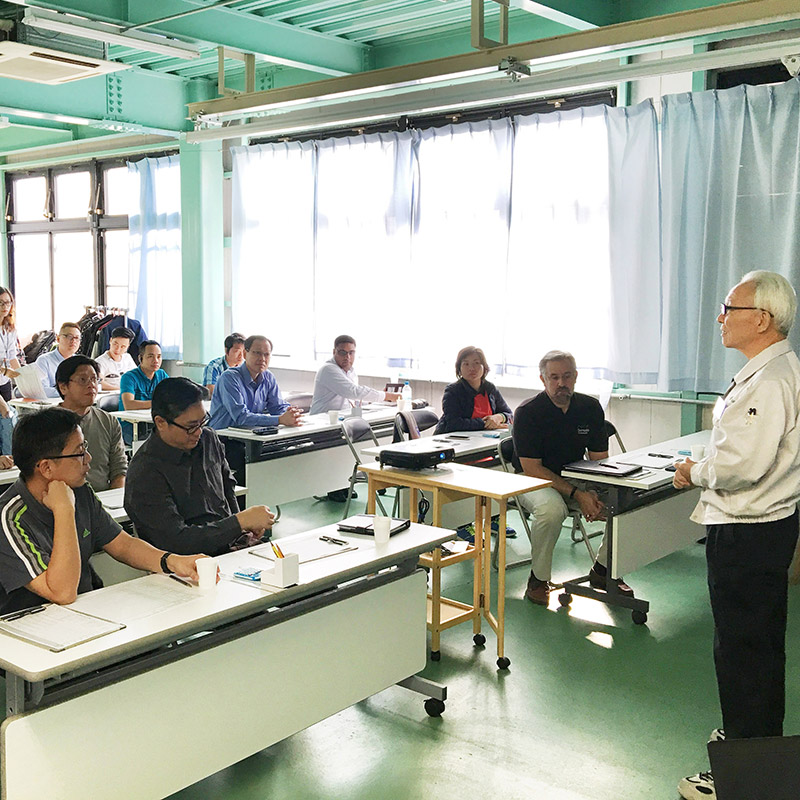
REASON 2
Consulting that shop floor workers
acknowledge our superiority and be pleased
In conventional consulting styles, there was a distance between consultant and the shop floor because it was promoted mainly consultant and management executives. Our consultant can provide a guidance without a distance between consultant and the shop floor through the guidance based on the “seeds of improvement” in a concrete way, instead of “finding fault” like a critic.
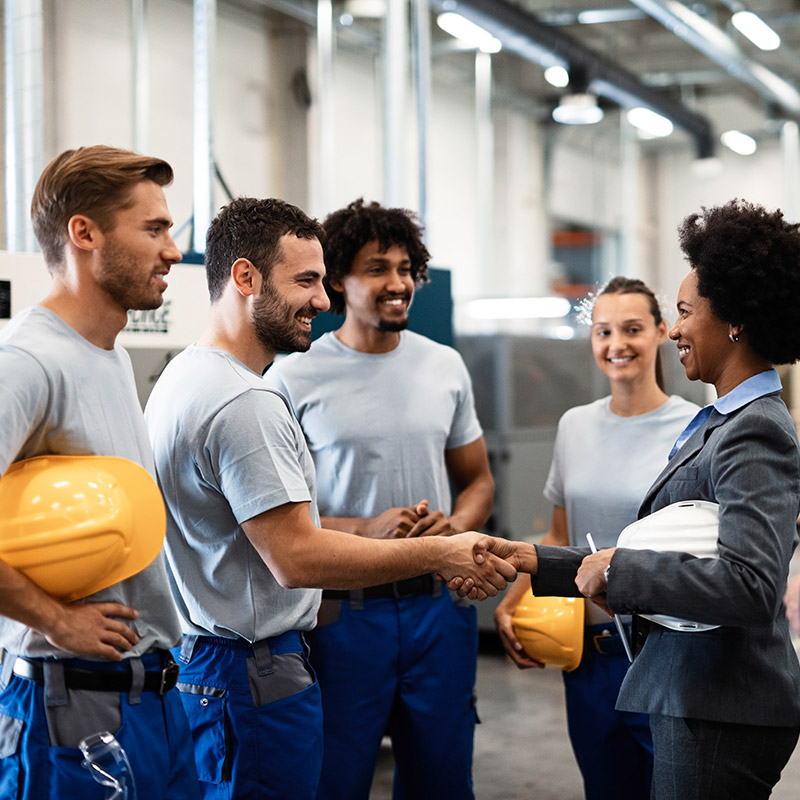
REASON 3
Continuous improvement will continue
even after the end of guidance
While strengthening “human resource development”, we focus on the “overall flow” from design to purchasing, manufacturing, logistics, and production control, and provide guidance that matches the actual situation of your company. Continuous improvement will continue even after the end of guidance through the guidance that is acceptable to the shop floor workers.
Consultants from major companies
with experience in over 40 countries will respond.
Please feel free to contact us.
If you are in a hurry, please call us.
(Japan time)
Open 08:30 – 17:30
Except for Saturday, Sunday, holidays, Year-End and New-Year holidays