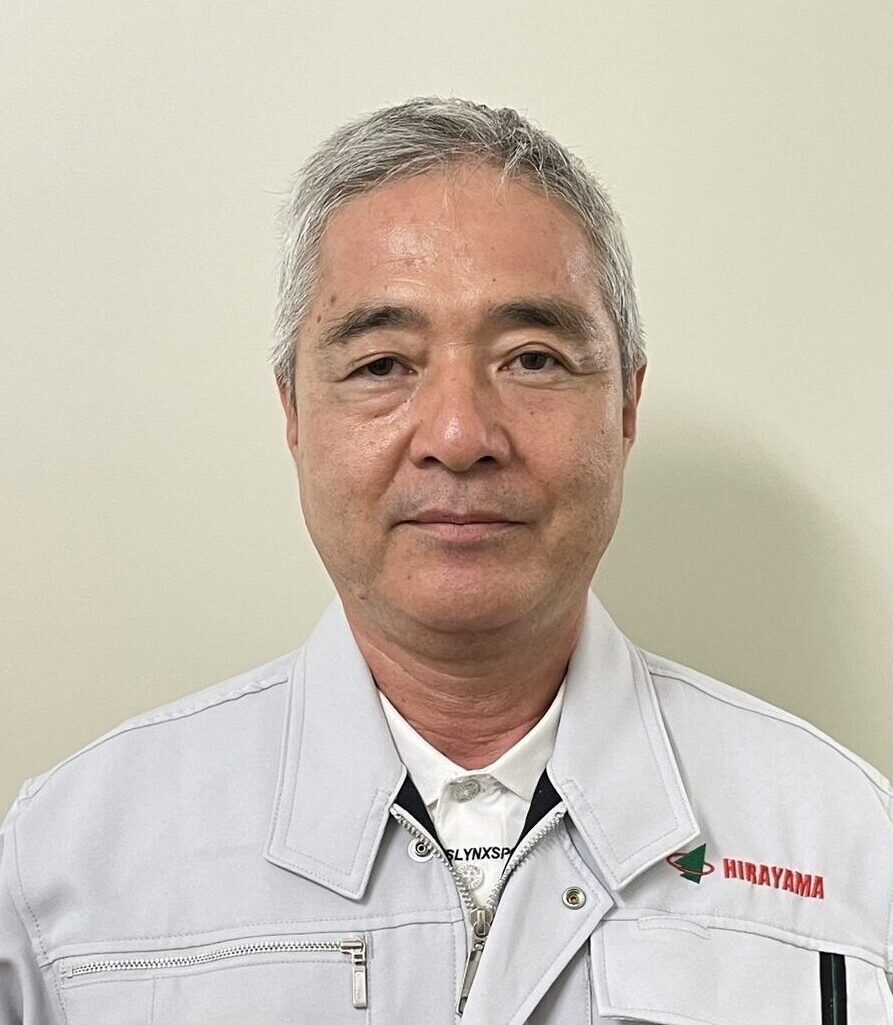
MATSUNAGA, Noboru
Matsunaga Noboru
After joining the welding section of the Toyota headquarters factory, he was assigned as an instructor and teacher at Toyota Technical Skills Academy
He was involved in the new vehicle models launching and was an essential skill trainer for production at both domestic and international sites
Career・Experience
Toyota Motor Corporation |
|
Hirayama |
Aiming to develop human resources to enhance on-site capabilities based on Toyota’s TWI (Training Within Industry) program |
Qualification |
|
Overseas Human Resource Development
United States, Mexico, Brazil, Argentina, Thailand, South Africa, and other countries
Consultants from major companies
with experience in over 40 countries will respond.
Please feel free to contact us.
If you are in a hurry, please call us.
(Japan time)
Except for Saturday, Sunday, holidays, Year-End and New-Year holidays
List of specialized consultants by purpose
人材育成TPSトレーナーその他Human development5SIE工場の立上げ支援コスト削減リードタイム短縮生産性向上品質向上経営改善tps生産技術Quality improvement Cost reductionProductivity improvementInventory controlLead time reductionSafety improvement Human resources developmentIotTPS trainerManagement improvement Equipment maintenanceProduction technologyDXOthers工場の立上げ支援3 reasons why we are chosen REASON
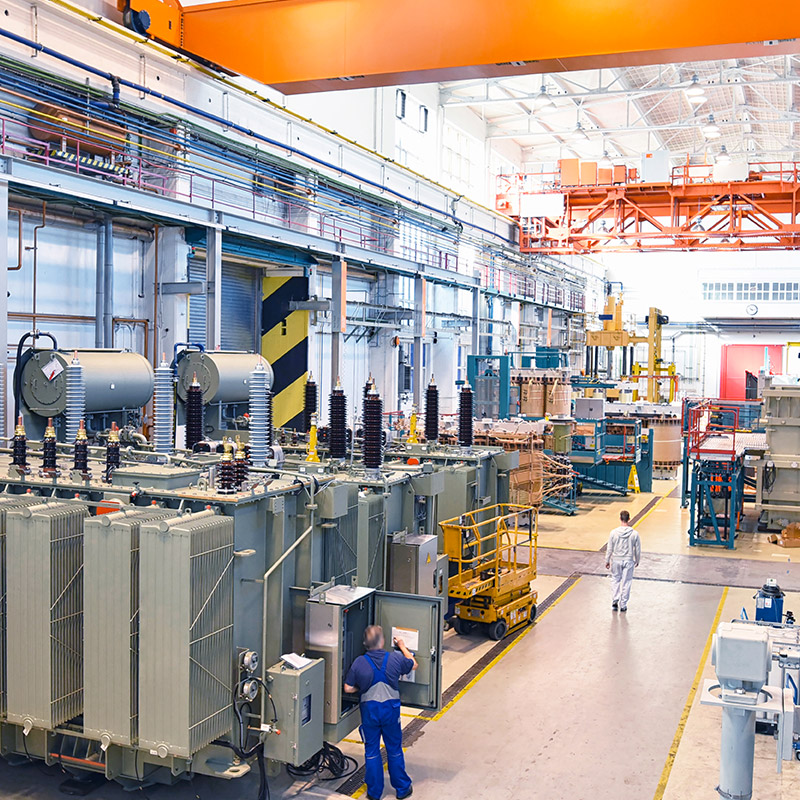
REASON 1
Improvement experience of
more than 1,500 companies in 40 countries
There must be the shop floor issues that cannot be solved by your own company alone. Improvements and reforms for manufacturing industry to survive, regardless of country or industry, need development of your human resources through practical experiences of improvement, and strengthening of your production system base.
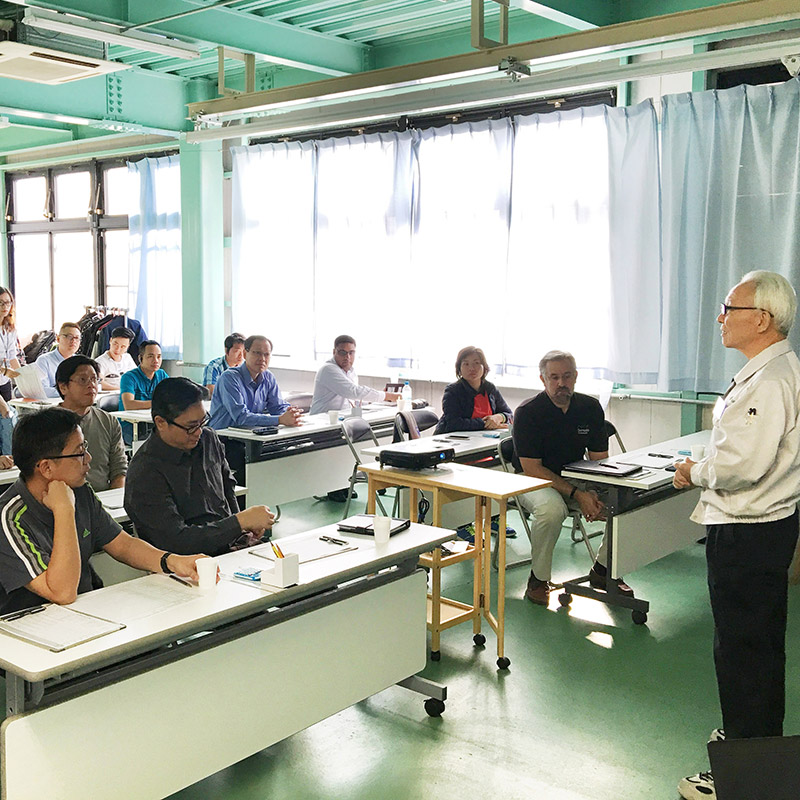
REASON 2
Consulting that shop floor workers
acknowledge our superiority and be pleased
In conventional consulting styles, there was a distance between consultant and the shop floor because it was promoted mainly consultant and management executives. Our consultant can provide a guidance without a distance between consultant and the shop floor through the guidance based on the “seeds of improvement” in a concrete way, instead of “finding fault” like a critic.
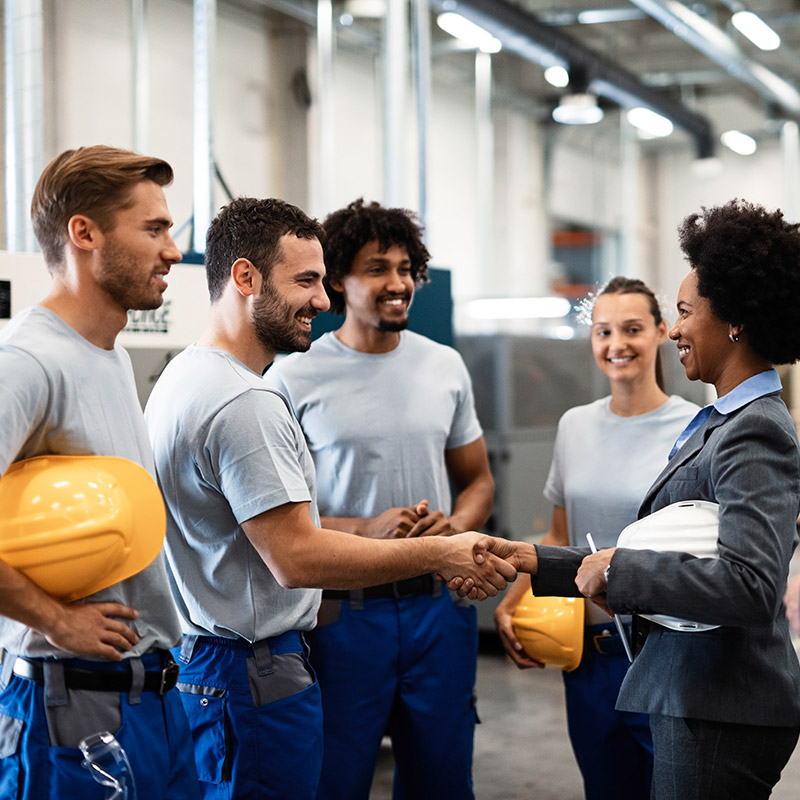
REASON 3
Continuous improvement will continue
even after the end of guidance
While strengthening “human resource development”, we focus on the “overall flow” from design to purchasing, manufacturing, logistics, and production control, and provide guidance that matches the actual situation of your company. Continuous improvement will continue even after the end of guidance through the guidance that is acceptable to the shop floor workers.