Pushpakumara, Thilak
TPM and Lean Management Consultant
Thilak has trained more than 50,000 executives and managers at different levels of 300 leading organizations in Sri Lanka and overseas.
Institute of Lean Management (Pvt) Ltd- Founder & the CEO of the Institute of Lean Management (Pvt) Ltd,
TPM and Lean Management Consultant and the Managing Director of Lean Solutions (Pvt) Ltd, Bangladesh.
Field of expertise
#Quality improvement #Cost reduction#Productivity improvement#Management improvement
Professional industry
#Automobile#Electric and electronic#Others
KAKIZAWA, Kouichi
Ricoh Co. - Quality Control Divison Introduced Toyota Production System in Ricoh after training for five years in Motomachi Plant of Toyota Motor Co.
At Ricoh, he launched a Ricoh Production System based on the Toyota Production System.
After that, he instructed other industries, such as food and confectionery industry and medical industry etc., on the Toyota Production System.
Field of expertise
#Quality improvement #Cost reduction#Productivity improvement#Lead time reduction#Safety improvement #Iot#Others
Professional industry
#Architecture / Construction#White collar#Warehouse logistics#Medicine#Food#Others
ISHIKAWA, Hisayoshi
Professional Engineer (Engineering management field)
Technical consultant for production technology, quality control, equipment maintenance and reliability improvement.
At the same time as improving manufacturing site,he develops human resources so that improvements can be made continuously at each manufacturing site.
Field of expertise
#Quality improvement #Productivity improvement#Human resources development# Equipment maintenance
Professional industry
#Automobile#White collar#Others
List of specialized consultants by purpose
人材育成TPSトレーナーその他Human development5SIE工場の立上げ支援コスト削減リードタイム短縮生産性向上品質向上経営改善Quality improvement Cost reductionProductivity improvementInventory controlLead time reductionSafety improvement Human resources developmentIotTPS trainerManagement improvement Equipment maintenanceProduction technologyDXOthers工場の立上げ支援
3 reasons why we are chosen
REASON
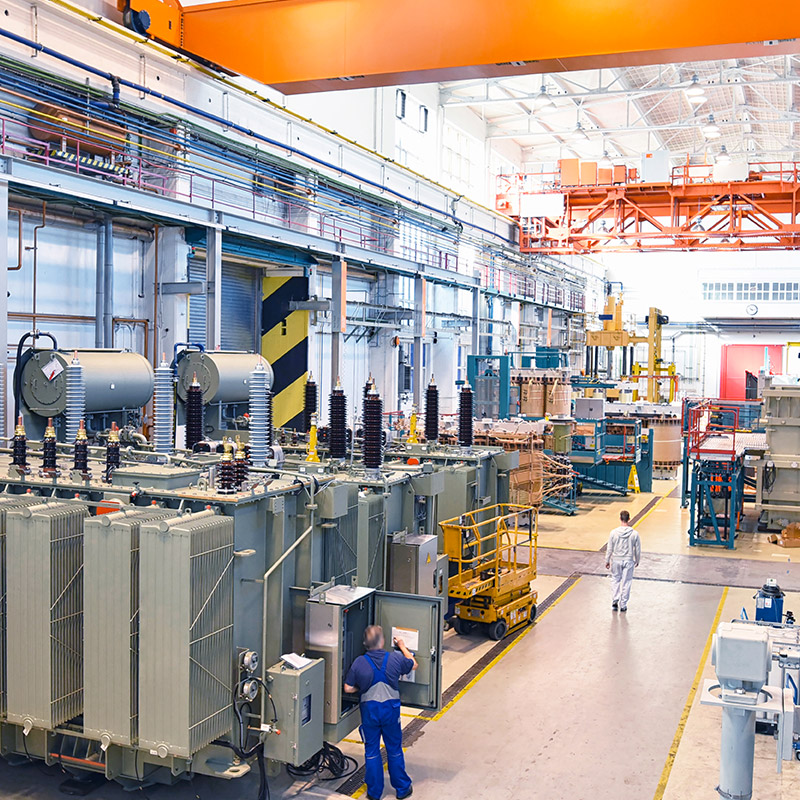
REASON 1
Improvement experience of
more than 1,500 companies in 40 countries
There must be the shop floor issues that cannot be solved by your own company alone. Improvements and reforms for manufacturing industry to survive, regardless of country or industry, need development of your human resources through practical experiences of improvement, and strengthening of your production system base.
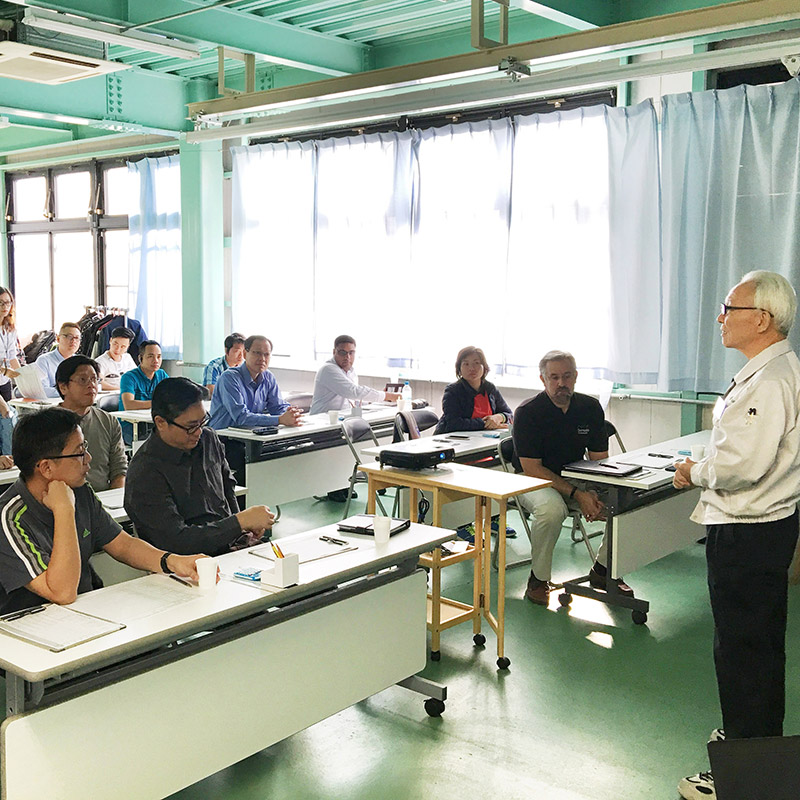
REASON 2
Consulting that shop floor workers
acknowledge our superiority and be pleased
In conventional consulting styles, there was a distance between consultant and the shop floor because it was promoted mainly consultant and management executives. Our consultant can provide a guidance without a distance between consultant and the shop floor through the guidance based on the “seeds of improvement” in a concrete way, instead of “finding fault” like a critic.
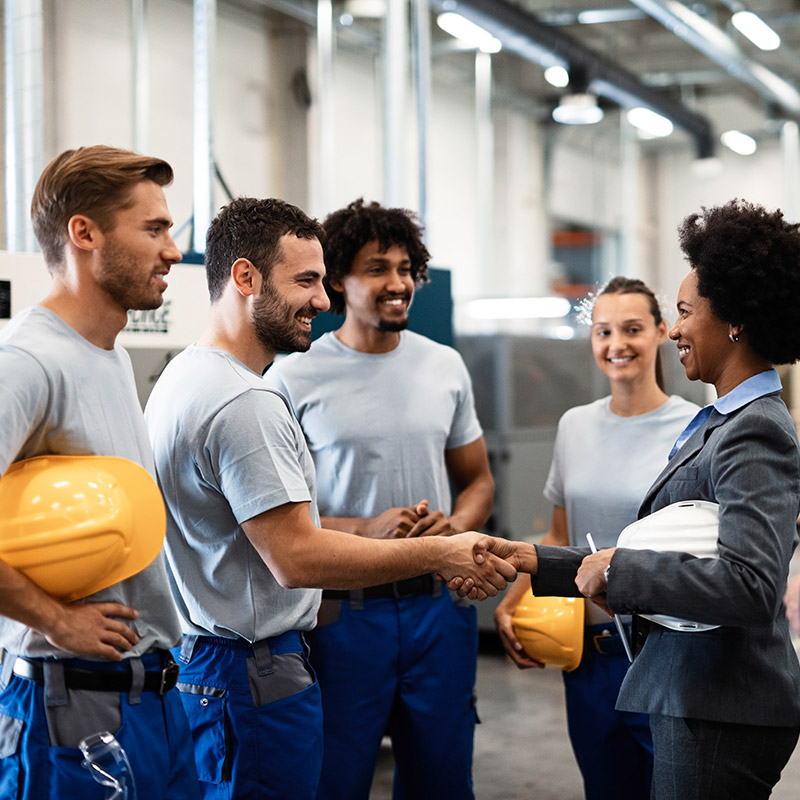
REASON 3
Continuous improvement will continue
even after the end of guidance
While strengthening “human resource development”, we focus on the “overall flow” from design to purchasing, manufacturing, logistics, and production control, and provide guidance that matches the actual situation of your company. Continuous improvement will continue even after the end of guidance through the guidance that is acceptable to the shop floor workers.
Consultants from major companies
with experience in over 40 countries will respond.
Please feel free to contact us.
If you are in a hurry, please call us.
(Japan time)
Open 08:30 – 17:30
Except for Saturday, Sunday, holidays, Year-End and New-Year holidays