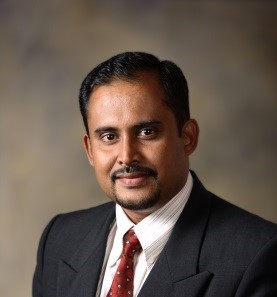
Pushpakumara, Thilak
Thilak Pushpakumara
Thilak has trained more than 50,000 executives and managers at different levels of 300 leading organizations in Sri Lanka and overseas.
Institute of Lean Management (Pvt) Ltd- Founder & the CEO of the Institute of Lean Management (Pvt) Ltd,
TPM and Lean Management Consultant and the Managing Director of Lean Solutions (Pvt) Ltd, Bangladesh.
Field of expertise
#Quality improvement #Cost reduction#Productivity improvement#Management improvement
Professional industry
#Automobile#Electric and electronic#Others
Thilak Pushpakumara is the founder & the CEO & of the Institute of Lean Management (Pvt) Ltd, a corporate trainer, TPM and Lean Management Consultant and the Managing Director of Lean Solutions (Pvt) Ltd, Bangladesh.
He has been certified on lean manufacturing at University of Michigan, MI, USA, and trained on lean supply chain, lean in service organization and lean in sales in Lean Enterprise Institute (LEI), USA and Lean Enterprise Academy, UK. He has participated knowledge sharing sessions with global lean leaders in USA, UK and Canada. He has been intensively trained in Japan on TPM, TQM, TPS and Company Wide Problem Solving and he is an expert in Toyota Production System.
He is a Japan Institute of Plant Maintenance (JIPM) accredited Total Productive Maintenance & Management (TPM) Instructor, certified Lean Master Black Belt and Lean Master Coach(Japan) and a certified trainer & facilitator on gaining change skills by Spenser Johnson Partners, USA.
He was trained by DuPont Safety Resources, USA on Managing Safety Systems that work for operations managers with audit training and also on train the trainer by internationally acclaimed Bob Pike Group, USA.
Thilak has 20 years of hands on experience acquired through success in a number of senior managerial positions in the field of manufacturing and has gained a wealth of experience working closely with world’s leading consultants in Japan and USA and currently global lean leaders in TPM and lean implementation at Unilever Sri Lanka and Loadstar Pvt. Ltd.
Thilak has trained more than 50,000 executives and managers at different levels of 300 leading organizations in Sri Lanka and overseas. He certified more than 1500 industry professionals as TPM practitioners, lean practitioners and advance 5S instructors in Sri Lanka and few from overseas. He has submitted technical papers on TPM, Lean and Quality Management for local and international forums. He is the founder of the Association of TPM Practitioners in Sri Lanka.
Thilak was Former General Manager, Productivity Improvement and Training & Development of Loadstar (Pvt) Ltd. and former Plant Manager, Unilever Sri Lanka. Currently functions as the CEO of the Institute of Lean Management (Pvt) Ltd and shared his experiences and the profound knowledge as corporate trainer & consultant with leading manufacturing organizations in Sri Lanka and overseas since 2009.
Consultants from major companies
with experience in over 40 countries will respond.
Please feel free to contact us.
If you are in a hurry, please call us.
(Japan time)
Except for Saturday, Sunday, holidays, Year-End and New-Year holidays
List of specialized consultants by purpose
人材育成TPSトレーナーその他Human development5SIE工場の立上げ支援コスト削減リードタイム短縮生産性向上品質向上経営改善Quality improvement Cost reductionProductivity improvementInventory controlLead time reductionSafety improvement Human resources developmentIotTPS trainerManagement improvement Equipment maintenanceProduction technologyDXOthers工場の立上げ支援3 reasons why we are chosen REASON
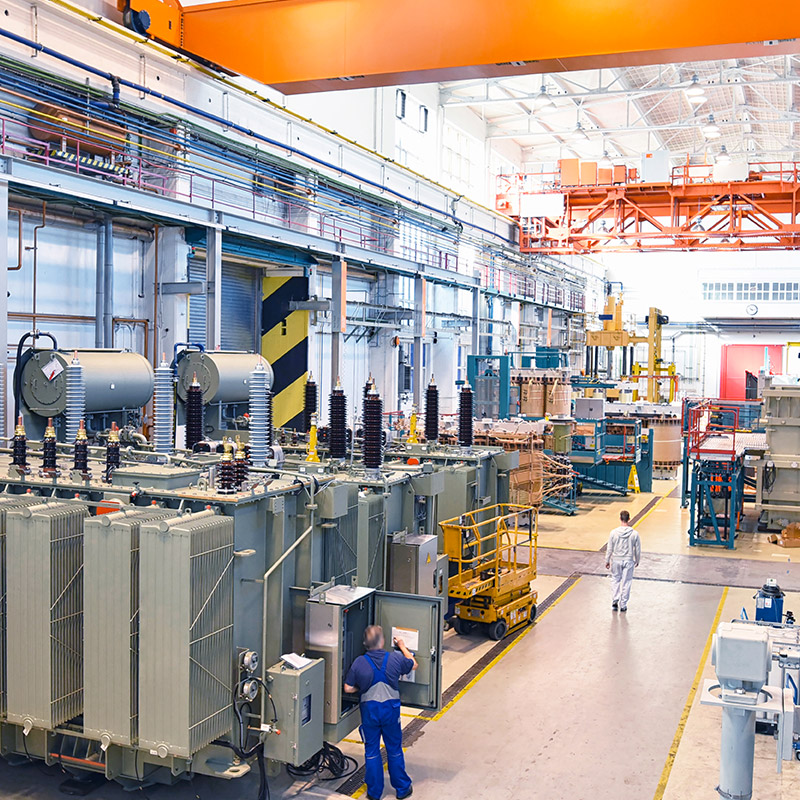
REASON 1
Improvement experience of
more than 1,500 companies in 40 countries
There must be the shop floor issues that cannot be solved by your own company alone. Improvements and reforms for manufacturing industry to survive, regardless of country or industry, need development of your human resources through practical experiences of improvement, and strengthening of your production system base.
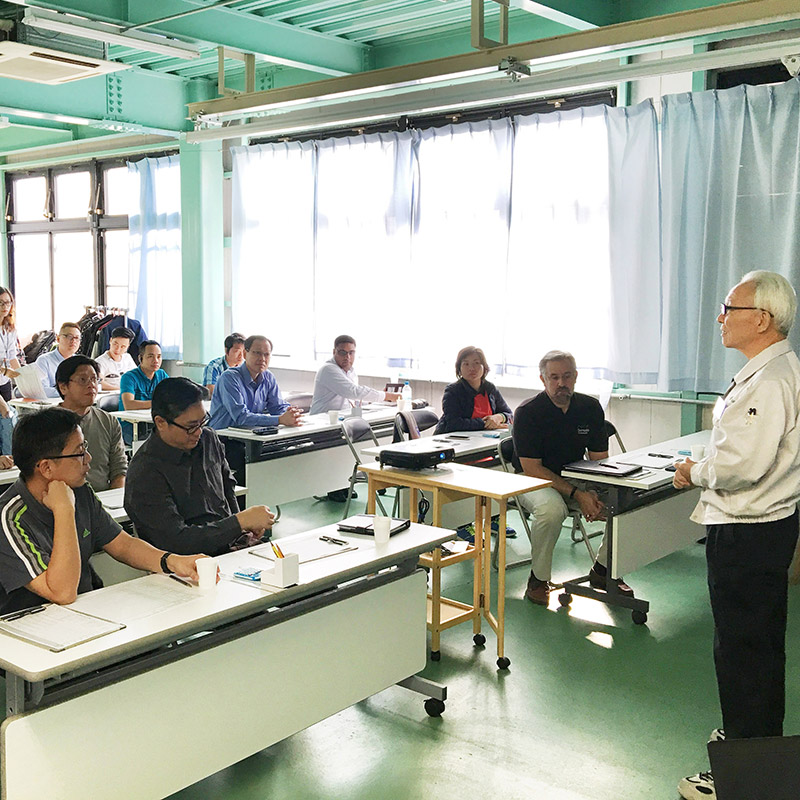
REASON 2
Consulting that shop floor workers
acknowledge our superiority and be pleased
In conventional consulting styles, there was a distance between consultant and the shop floor because it was promoted mainly consultant and management executives. Our consultant can provide a guidance without a distance between consultant and the shop floor through the guidance based on the “seeds of improvement” in a concrete way, instead of “finding fault” like a critic.
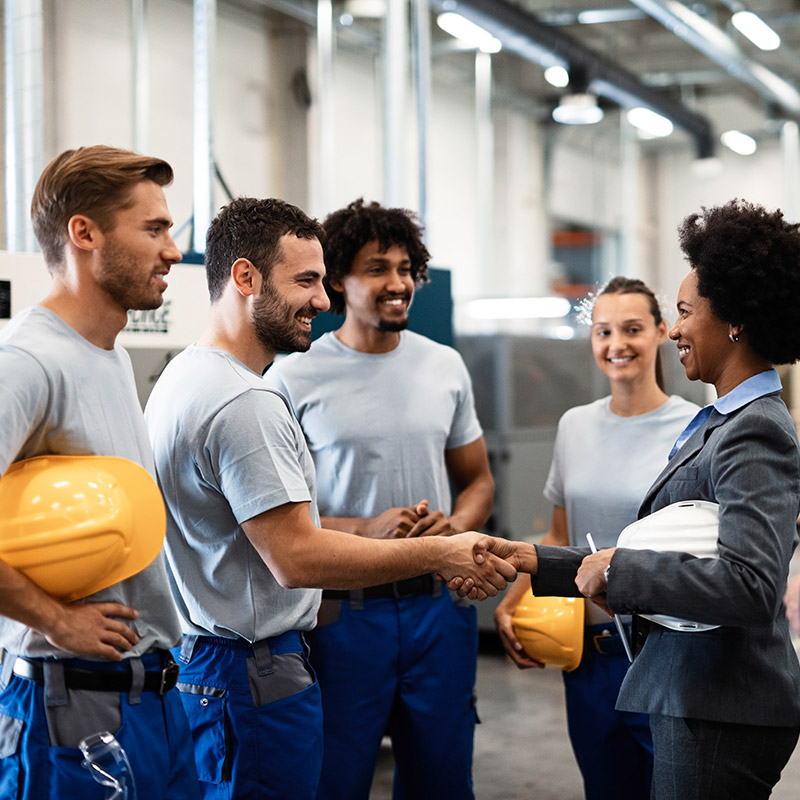
REASON 3
Continuous improvement will continue
even after the end of guidance
While strengthening “human resource development”, we focus on the “overall flow” from design to purchasing, manufacturing, logistics, and production control, and provide guidance that matches the actual situation of your company. Continuous improvement will continue even after the end of guidance through the guidance that is acceptable to the shop floor workers.