Our team is composed of Professionals with experience obtained through work in the most representative Japanese Manufacturing Companies.
List of specialized consultants by purpose
人材育成TPSトレーナーその他Human development5SIE工場の立上げ支援コスト削減リードタイム短縮生産性向上品質向上経営改善Quality improvement Cost reductionProductivity improvementInventory controlLead time reductionSafety improvement Human resources developmentIotTPS trainerManagement improvement Equipment maintenanceProduction technologyDXOthers工場の立上げ支援Toshio Takeuchi
Gemba Kaizen (work-site improvement) Consultant
Tokai Rika Co., Ltd. (OB)
Areas of expertise are innovation instructions for production department, indirect department, production management department, and logistics systems.
Takeshi Kawabata
Former DENSO Corp. Production Engineering Division
Learned and implemented the Toyota Production System directly from Toyota Motor Corporation. Also experienced in two new factory constructions and one existing factory renovation, managing construction schedules and budgets as planned, and realizing information and logistics optimization from the factory entrance to exit.
Responsible for the construction of Japan's largest single factory building at the time, covering 120,000 sqm.
Field of expertise
#Others#工場の立上げ支援
Professional industry
#Automobile#Electric and electronic#Metal#Others
MATSUNAGA, Noboru
Toyota Motor Corporation OB, Headquarters Factory Group Leader (GL)
After joining the welding section of the Toyota headquarters factory, he was assigned as an instructor and teacher at Toyota Technical Skills Academy
He was involved in the new vehicle models launching and was an essential skill trainer for production at both domestic and international sites
MASAFUMI, Tanaka
Toyota Motor Corporation OB, Headquarters Factory Group Leader (GL)
After gaining experience in assembly line operations, operational management, and support for vehicle production in Asia at the head office plant, I transferred to the Human Resources department (in charge of overall training and development), where I was involved in various training programs, planning and management, and the training and development of trainers for company-wide workshops.
Nobutoshi Nagaya
Former Toyota Motor East Japan, Inc.: Technical Supervisor & Advisor, in charge of PS (Production System) and TQM (Total Quality Management) projects.
Former Kanto Auto Works: Executive Managing Director, Deputy Head of Production Technology Division, in charge of overseeing overseas business.
Directly learned the essence of TPS (Toyota Production System) from Shin Uchikawa, one of the four lieutenants of Taiichi Ohno, former Vice President. Handled the introduction of the Toyota Production System to various companies both domestically and internationally.
Professional industry
#Automobile
Miyuky Honda
Manager of Consulting Division
Mr. Honda has over 20 years of experience with overseas accounts in Japan.
KOJIMA, Kazuhiro
Digital Innovation/Information Technology Design /Digital Transformation Consultant
A consultant at the forefront of practical implementation, specialized in cutting-edge technologies such as AI, RPA, low-code, IoT, and data science.
With a Master's degree from the University of Tokyo, it is leveraged by profound knowledge and experience to lead in the realms of DX and generative AI. The insights and practical approaches have been recognized and highly esteemed in prestigious forums, including invited lectures at the University of Tokyo's Center for Manufacturing Management and the Japan Warehousing Association.
Field of expertise
#DX
Professional industry
#DI/IT/ DX
Tsuyoshi Ishigamori
Safety and Health Management Consultant
As a full-time health and safety officer, He worked with a major manufacturing company for disaster prevention and health hazard prevention for 15 years. In safety management, He has enhanced activities to reduce the 1,000-person rate, frequency rate, and strength rate, and are in charge of foreman education and new graduate education instructors as RST. In Safety management, the obligations of business owners after conducting health examinations and stress checks have become established. In addition, based on his experience in personnel and general affairs, we explained the Labor Standards Law, the Industrial Safety and Health Law, and related laws and regulations by rank, and enhanced the system to prevent mental insufficiency due to long working hours. We will continue to make efforts so that business owners will not be questioned by the "safety consideration obligation".
Pushpakumara, Thilak
TPM and Lean Management Consultant
Thilak has trained more than 50,000 executives and managers at different levels of 300 leading organizations in Sri Lanka and overseas.
Institute of Lean Management (Pvt) Ltd- Founder & the CEO of the Institute of Lean Management (Pvt) Ltd,
TPM and Lean Management Consultant and the Managing Director of Lean Solutions (Pvt) Ltd, Bangladesh.
Field of expertise
#Quality improvement #Cost reduction#Productivity improvement#Management improvement
Professional industry
#Automobile#Electric and electronic#Others
Tomohiro Suzuki
Former employee of Japan Tobacco Inc., Technical Development Department, Manufacturing Department
Field of expertise
#Human resources development#Production technology
Professional industry
#Chemistry#Others
List of specialized consultants by purpose
人材育成TPSトレーナーその他Human development5SIE工場の立上げ支援コスト削減リードタイム短縮生産性向上品質向上経営改善Quality improvement Cost reductionProductivity improvementInventory controlLead time reductionSafety improvement Human resources developmentIotTPS trainerManagement improvement Equipment maintenanceProduction technologyDXOthers工場の立上げ支援
3 reasons why we are chosen
REASON
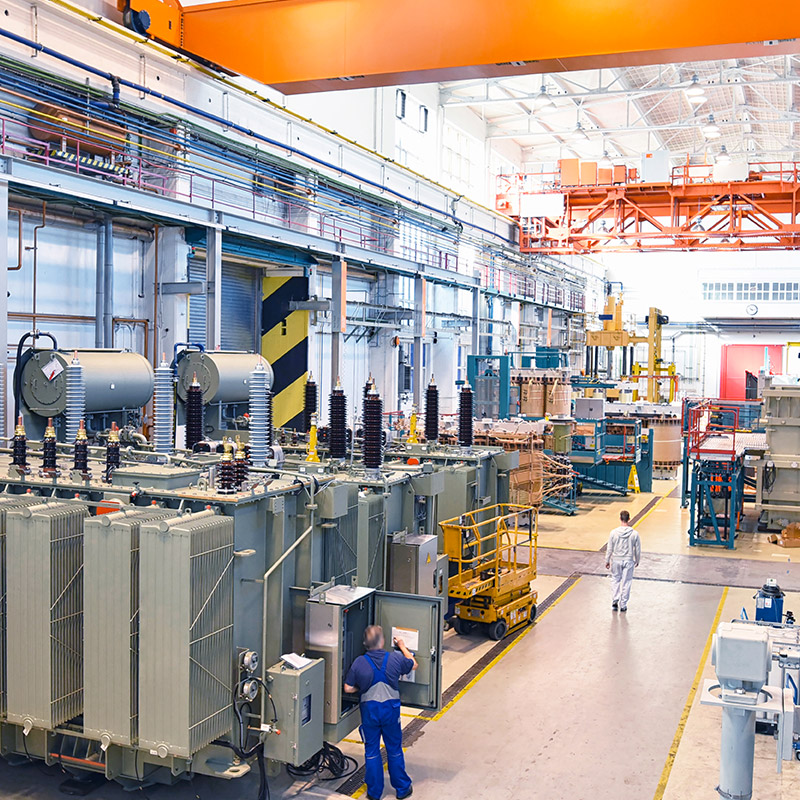
REASON 1
Improvement experience of
more than 1,500 companies in 40 countries
There must be the shop floor issues that cannot be solved by your own company alone. Improvements and reforms for manufacturing industry to survive, regardless of country or industry, need development of your human resources through practical experiences of improvement, and strengthening of your production system base.
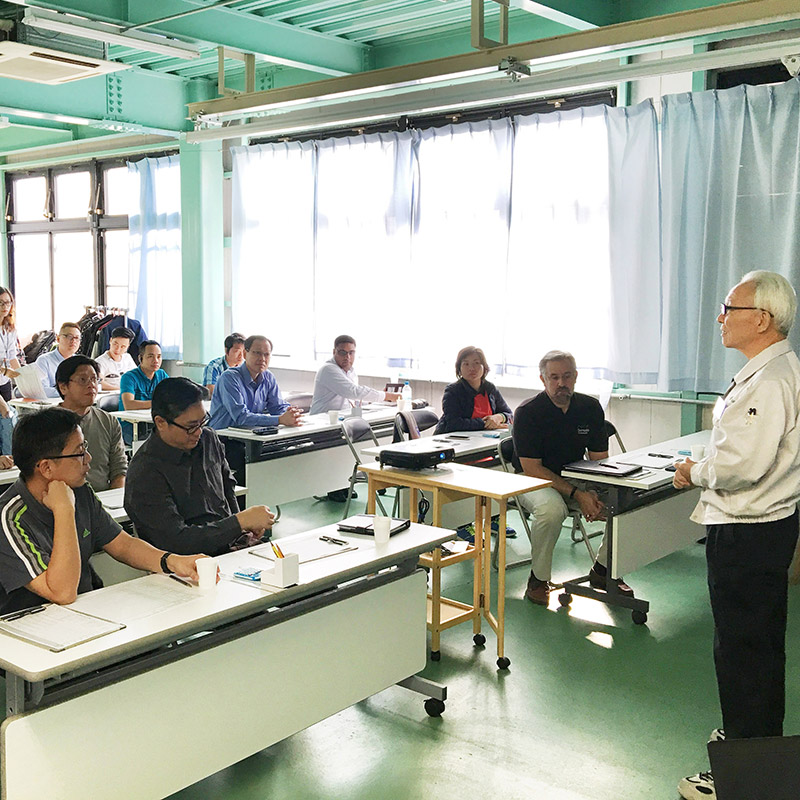
REASON 2
Consulting that shop floor workers
acknowledge our superiority and be pleased
In conventional consulting styles, there was a distance between consultant and the shop floor because it was promoted mainly consultant and management executives. Our consultant can provide a guidance without a distance between consultant and the shop floor through the guidance based on the “seeds of improvement” in a concrete way, instead of “finding fault” like a critic.
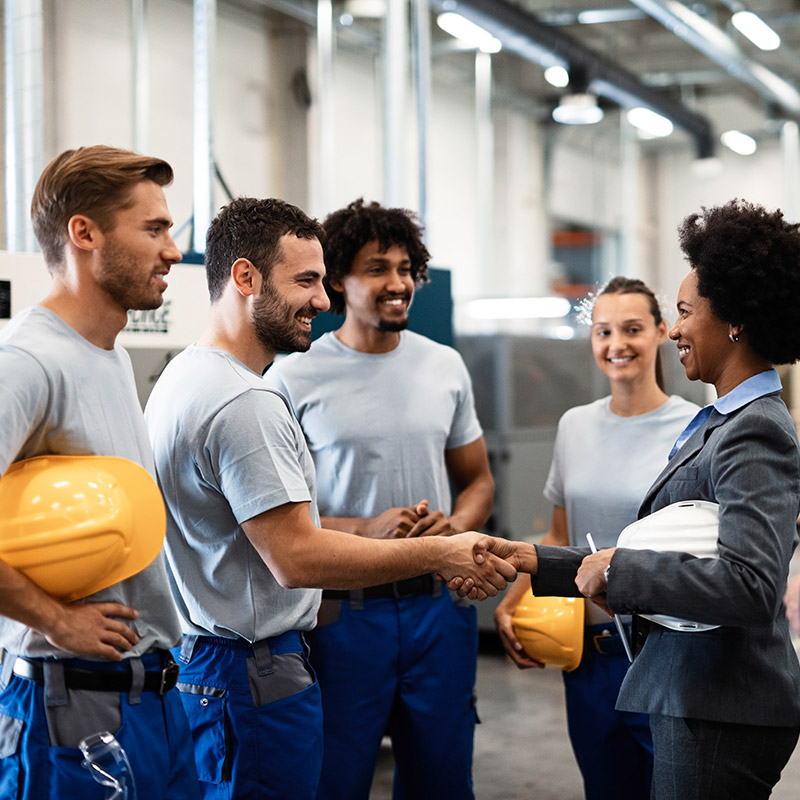
REASON 3
Continuous improvement will continue
even after the end of guidance
While strengthening “human resource development”, we focus on the “overall flow” from design to purchasing, manufacturing, logistics, and production control, and provide guidance that matches the actual situation of your company. Continuous improvement will continue even after the end of guidance through the guidance that is acceptable to the shop floor workers.
Consultants from major companies
with experience in over 40 countries will respond.
Please feel free to contact us.
If you are in a hurry, please call us.
(Japan time)
Open 08:30 – 17:30
Except for Saturday, Sunday, holidays, Year-End and New-Year holidays